ALKALİ ÇİNKO - NİKEL BANYOSU
EKİPMANLAR:
Tank | Çelik, PP veya PVC |
Çinko destek tankı | Banyodaki çözelti konsantrasyonunu sabit tutmak için gereklidir. Çelik veya çelik plakalarla kaplanmış plastik tank kullanılabilir. Çinko destek tankının hacmi banyonun toplam hacminin % 15-20 ‘si kadar olmalıdır. Çelik sepetler içinde çinko anotlar kullanılmalıdır. Anot miktarı arzulanan konsantrasyona göre değişiklik gösterebilir. Çinko destek tankından banyoya besleme mutlaka filtre edilerek yapılmalıdır. |
Soğutma/Isıtma | Çelik; Sıcaklık dağılımı kontrolü sabit alaşım kompozisyonu sağlamak için gereklidir. |
Filtrasyon | Sürekli filtrasyon tavsiye edilir. Bir saatte, banyo 2-3 defa çevrilmelidir. |
Hareket | Katot hareketi 4-6 m/dk Dolap dönüşü 3-10 devir/dk olmalıdır. Hava hareketi kullanılmaz. |
Anot | 10-15 cm genişlikte ve 10 mm kalınlıkta nikel anot kullanılmalıdır. Nikel kaplanmış çelik anot kullanılamaz. |
Anot/katot | 1:1- 2:1 |
Havalandırma | Gereklidir. |
ÇALIŞMA ŞARTLARI:
Parametreler | | Birim | Aralık | Optimum |
Katodik akım yoğunluğu | Askı | A/dm² | 1-3 | 1,8 |
| Dolap | A/dm² | 0,5-1,0 | 0,8 |
| | | | |
Gerilim | Askı | V | 8 - 12 | |
| Dolap | V | 12 - 18 | |
| | | | |
Katot verimi | | % | 50-60 | |
Kaplama hızı ( 1,5 A/dm² ile) | | µm/dak | yaklaşık: 0,2 | |
Anodik akım yoğunluğu | | A/dm² | 1-10 | 8 |
Anot/Katot oranı | | - | 1 / 4 - 1 / 6 | 1 / 5 |
Sıcaklık | | °C | 21-25 | 23 ± 1,0 |
Düşük akımda selektif | | Kötü kaplama durumunda (0,1- 0,2 A/dm²) ile birkaç saat ( tercihen minimum 0,5 Ah/L) |
BAKIM:
Sürekli olarak iyi sonuçlar sağlamak için küçük fakat sık sık ilaveler yapılmasını öneriyoruz. Eğer parlaklık hızla düşerse, büyük oranlarda ilaveler yapmadan önce, banyoyu normal şartlara getirmek için banyo çözeltisinin kimyasal analizinin yapılmasını öneriyoruz.
Banyonun belirli periyotlarda analiz edilmesi gerekmektedir(minimum günde bir defa). Analiz yapıldıktan sonra eksilen çinko, çinko destek tankından, sodyum hidroksit, eritilerek ve nikel de Nikel Besleme çözeltisi ile beslemelidir. Banyonun analiz ile kontrolü ve ilavelerin küçük miktarlarda yapılması aynı kalitede ürün almak için önemlidir.
Her alkali banyoda olduğu gibi çinko-nikel banyosunda da zamanla karbonat oluşur. Oluşan karbonat banyoda verimi düşürecek yönde etkili olur. Sodyum karbonat konsantrasyonu 60 g/l mertebesine çıktığında banyo soğutularak süzülmeli ve böylelikle oluşan karbonat uzaklaştırılmalıdır.
Eksilen Çinkonun Tamamlanması:
Tesiste kaplama tankının en az 1/5 büyüklüğünde ayrı bir çinko zenginleştirme tankı olmalıdır. Bunun içinde 140 g/l sodyum hidroksit çözeltisi hazırlanır ve içine mümkün olduğunca çok sayıda ve menevişlendirilmiş demir sepetlerde çinko külçe konulur. Çinko külçeler bu çözeltide eriyerek zengin bir çinko çözeltisi oluşturur. Banyonun filtresi yardımıyla banyo çözeltisinin gerekli miktarı bu çözeltiyle yer değiştirilerek gerekli çinko seviyesi korunmuş olur.
İŞLEM SIRASI:
- Alkali sıcak yağalma
- Yıkama
- Asitleme ( HCl 1:1)
- Yıkama
- Elektrikli yağalma(anodik)
- Yıkama
- Asitleme (HCl 5% Hacimce)
- Yıkama
- Nötralizasyon
- Çinko-Nikel kaplama
- Yıkama
- Yıkama
- Asitleme (HCl 0,3 Hacimce%)
- Yıkama
- Pasivasyon
- Kurutma
Otomotiv sektöründe devamlı yükselen garanti sürelerine cevap olarak Çinko ve düşük Çinko alaşımları(Zn-Co ve Zn-Fe) yerine 5 kat daha fazla korozyon dayanımı sergileyen Zn-Ni günümüzde vazgeçilmez alternatif haline gelmektedir. En az 5-6 yıl paslanmama özelliğini taşıyan Zn-Ni kaplama diğer sektörlerde de tercih merceği olmaktadır. Proses asitli ve alkali olarak iki farklı bazlı çalışmaktadır.
Yüksek sıcaklıkta çalışan parçalar için mükemmel yapışma ve yüksek korozyon direncinde Çinko Nikel alaşımlı kaplama tartışmasız en iyi prosestir. Orijinal olarak yaklaşık 20 yıl önce kullanılmaya başlanan proses, günümüz teknolojisinde geliştirilmiş ve bir çok aplikasyonlarda banyo hakimiyeti, kaplama kalitesi ve görüntüsü düşük amper sahalarında mükemmel dağılımı ile özellikle otomotiv üreticileri için vazgeçilmez bir alternatif olmuştur.
Alkali Siyanür İçermeyen Çinko – Nikel Alaşımlı Kaplamalar
Çinko kaplama, oldukça uzun yıllardır demir esaslı malzemelerden imal fonksiyonel parçalar üzerine katodik koruma amaçlı kullanılmaktadır. Katodik koruma etkisinin mekanizması incelendikçe çinko kaplamaların alaşımlandırılarak korozyon dayanımında artışlar elde edilmiş ve sırasıyla çinko - kobalt, çinko - demir ve çinko - nikel kaplama türleri geliştirilmiştir. Bu alaşımlı kaplamalar arasında en yüksek korozyon direnci çinko – nikel alaşımlı kaplamalarla elde edilmektedir. Alaşımsız çinko kaplamalara ve diğer alaşımlı çinko kaplamalara göre nötral tuz sprey testinde (ASTM B 117, DIN 50021) çinko nikel alaşımlı kaplamaların korozyon performanslarını tablo 1 de görebilirsiniz.
Tablo 1; çinko ve alaşımlı çinko kaplamaların korozyon performansları
Kaplama türü | Korozyon Performansı (1 mikrometre kaplama) (saat-kırmızı pas) |
Çinko | 10 |
Çinko-Demir | 20 |
Çinko-Kobalt | 10 |
Çinko-Nikel (%12-15) | 100 |
Çinko nikel alaşımlı kaplamalar halen sanayide alkali ve asidik karakterli olmak üzere iki farklı elektrolitle kaplanmaktadır. İlk geliştirilen asidik karakterli çinko – nikel alaşımlı kaplama elektrolitleri gerek işlem parametrelerinin dar aralıkta çalışmasından gerekse korozyon direnci dışındaki bazı teknik özelliklerinin (metal dağılımı, süneklik) yetersiz kalmasından dolayı yerini günümüzde alkali karakterli çinko – nikel kaplama elektrolitlerine bırakmıştır. Halen sadece çok özel uygulamalar hariç çinko – nikel alaşımlı kaplamaların büyük bir çoğunluğu alkali karakterli elektrolitler ile yapılmaktadır.
Avrupa Birliğinin ömrünü doldurmuş araçlarla ilgili direktifleri doğrultusunda çinko ve alaşımlı çinko kaplamalar üzerine uygulanan altı değerlikli krom içeren pasivasyon uygulamaları yasaklanmıştır. Alternatif olarak sunulan altı değerlikli krom içermeyen uygulamalarda her ne kadar altı değerlikli uygulamalar kadar beyaz pas korozyon dayanımları elde edilse de altı değerlikli pasivasyon tabakalarının sahip olduğu kendi kendini iyileştirme etkisi maalesef altı değerlikli krom içermeyen pasivasyon tabakalarında geliştirilememiştir. Bu durum özellikle emniyet riski taşıyan otomotiv parçalarında ve motor bloğu yakınlarında bulunan ömrü boyunca nispeten yüksek sıcaklık ortamında çalışan otomotiv parçalarında çinko-nikel alaşımlı kaplamalara doğru bir talep yaratmıştır.
Şekil 1 de 8 mikrometre kromatlamasız çinko nikel alaşımlı kaplamaların içerdiği nikel oranına göre korozyon performanslarını görebilirsiniz.
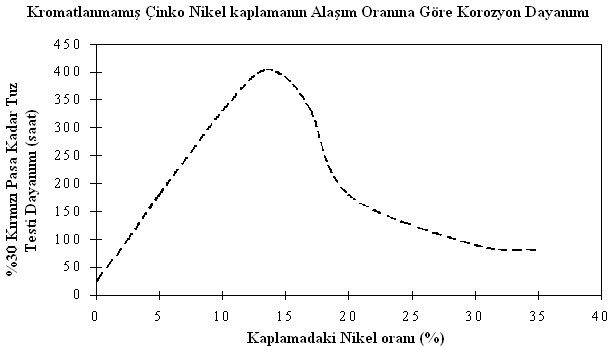
Alkali çinko nikel alaşımlı kaplama tekniği:
Alkali çinko nikel kaplama elektrolitleri, alkali siyanür içermeyen alaşımsız çinko kaplama elektrolitlerini temel almaktadır. Farklı olarak alkali ortamda çözünürlüğü çok düşük olan (çözünmeyen) nikelin çözünmesi için kompleksan ilavesi ve elektrolitik olarak kaplanan nikelin idamesi için nikel katkısı içermektedir.
Alaşımlı kaplamalar söz konusu olduğunda kimyasal kontrol yöntemlerinin ve tekniğinin önemli olduğu bilinmelidir. Özellikle çinko nikel alaşımlı kaplamalarda nikelin alaşım içerisindeki oranının %15'i geçmesi durumunda katodik koruma etkisi tersine dönerek anodik korozyon etkisine sebep olmaktadır. Diğer bir deyişle alaşım oranını %15'ten yüksek olması kaplanan parçanın beklenenden çok daha kısa bir sürede kırmızı pas görmesine neden olmaktadır. Özellikle kromatlama sonrası çinko nikel alaşımlı kaplamanın yüzeyindeki nikel oranında %0,5 ile %1 arasında artış kaydedilmesinden dolayı beklenen korozyon performansının riske atılmaması için kaplama işleminde hedef alaşım oranının %14 olarak belirlenmesi gerekmektedir.
Sürekli olarak seri üretim şartlarında hedef nikel alaşım oranın dar aralığında kaplama yapabilmek için standart volumetrik analiz yöntemlerinin yanında gelişmiş X-ışınımı ile kalınlık ve alaşım oranın analiz eden cihazların kullanılması gerekmektedir. Alaşım oranını etkileyen bir diğer faktör de elektrolit sıcaklığıdır. Her ne kadar elektrolit sıcaklığının yüksek olması alaşım oranını akım yoğunluklarına göre eş dağılımlı hale getirse de (şekil 2) metal kaplama dağılımını kötü yönde etkilemektedir (şekil 3).
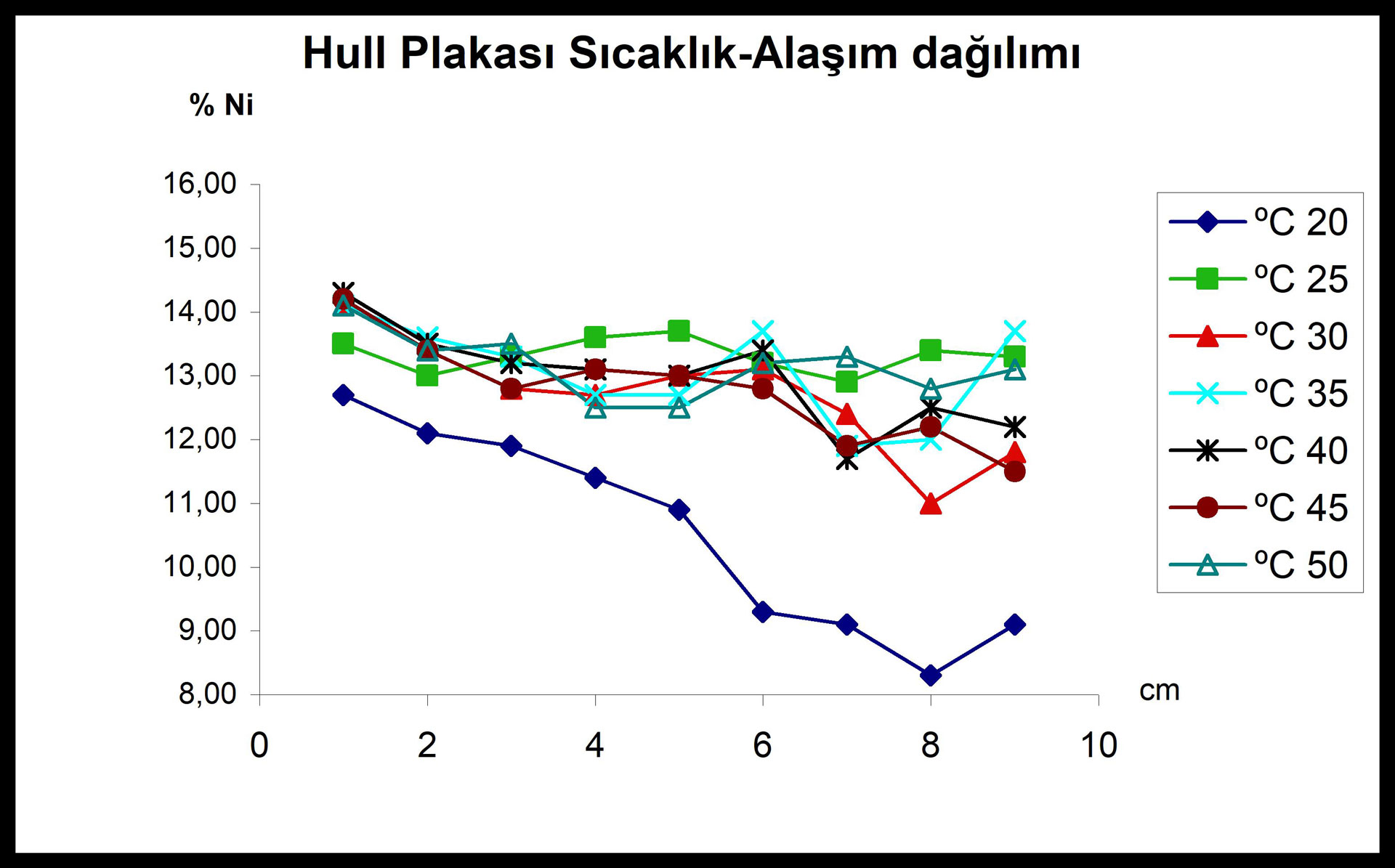
Şekil 2 : Hull plakası sıcaklık alaşım dağılımı grafiği
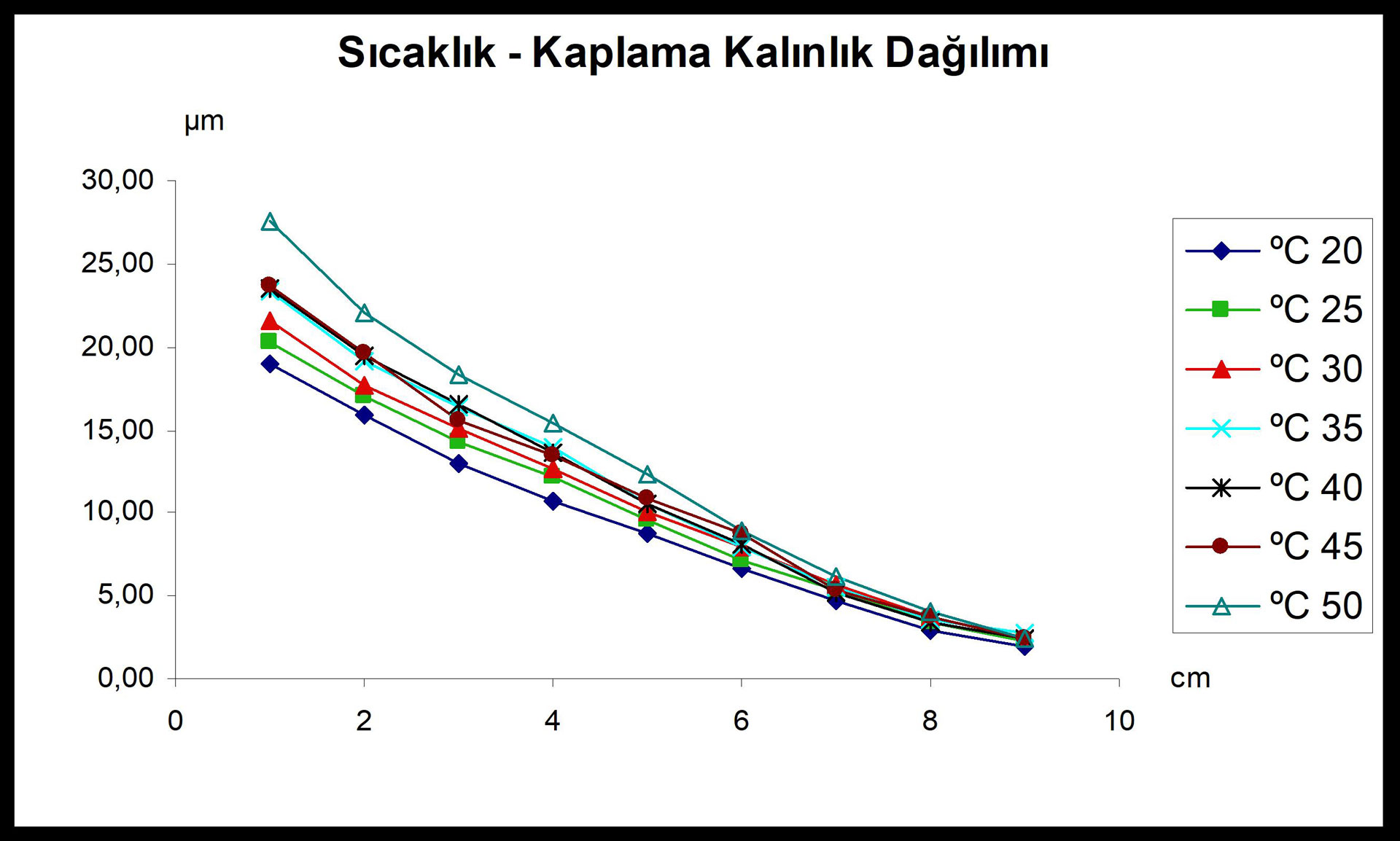
Kontrol altında tutulan elektrolit kompozisyonu ve kaplama parametreleri standart üretim için gerekli gözükmektedir. Fakat elektrolitin yaşına bağlı olarak içerisinde birikim gösteren kirlilikler de performans açısından riskler oluşturmaktadır. Bu kirliliklerin başında nikel katkısı ile elektrolite karışan sülfat gelmektedir. Ayrıca kompleksan katkısının elektroliz şartlarında parçalanarak kirlilik oluşturduğu bilinmektedir. Bunlara ilave olarak karbonat oluşumu da katodik akım verimini düşürmektedir.
Tüm bu olumsuz faktörler alkali siyanürsüz çinko-nikel kaplama elektrolitlerinin yaşlandıkça kaplama hızının düşmesine ve çalışma maliyetinin artmasına neden olmaktadır.
Alkali çinko nikel alaşımlı kaplama çalışma ekonomisi:
Katodik akım verimine bağlı olarak çinko-nikel alaşımlı kaplamanın kaplama hızı değişmektedir. Başka açıdan baktığımızda 10.000 Amper.saat çalışma sonucunda göreceli olarak taze elektrolitle yaklaşık 11 parça kaplanırken yaşlı elektrolitle ancak 5,5 parça kaplanabilmektedir. Şekil 3'te farklı alaşım oranlarında alkali çinko – nikel kaplama elektrolitlerinin katodik akım verimine bağlı olarak nikel katkısı harcama miktarlarını bulabilirsiniz.
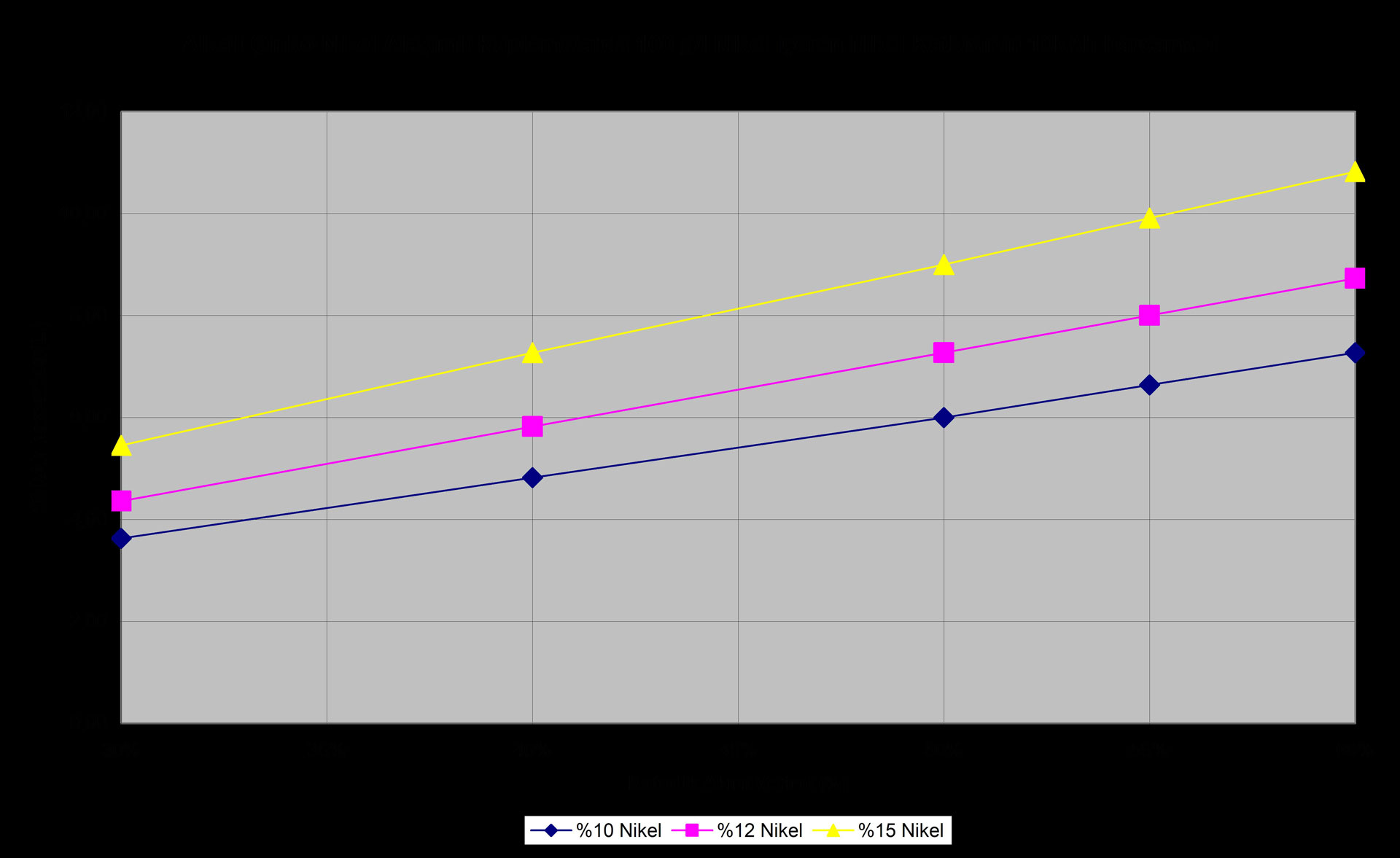
Şekil 3: muhtelif alaşım oranlarında alkali çinko – nikel kaplama elektrolitlerinin katodik akım verimine bağlı olarak nikel katkısı harcama grafiği
Çalışma ekonomisini oluşturmak için elektrolit kompozisyonunda kirlilik oluşturan faktörlerin kontrol altında tutulması mümkündür.
Alkali ortamlarda sodyum sülfatın, potasyum sülfata göre çözünürlüğü çok daha yüksektir. Sodyum hidroksit bazlı alkali çinko-nikel kaplama elektrolitlerinde sülfat zamanla birikme yaparak sorun yaratırken potasyum hidroksit bazlı elektrolitlerde bu sorunun oluşmadığı bilinmektedir. Dolayısıyla potasyum hidroksit bazlı alkali çinko-nikel kaplama elektrolitleri sülfat birikimi açısından çok daha avantajlıdır. Bir diğer husus da karbonatlaşmadır. Sodyum hidroksit bazlı elektrolitlerde, elektrolit dondurularak karbonat çözünürlüğü düşürülmekte ve çökelti olarak çözeltiden uzaklaştırılmaktadır. Bu işlem için dekarbonizasyon ünitesi gerekmektedir. Potasyum hidroksit bazlı elektrolitlerde de karbonat oluşmaktadır fakat karbonat oluşumu dış taşınmaya bağlı olarak çok nadiren yüksek olan üst limite yaklaşmaktadır. Potasyum hidroksit bazlı alkali çinko-nikel ve çinko kaplama elektrolitlerinde potasyum karbonat kaynaklı katodik akım verimi düşme sorununa henüz rastlanmamıştır. Çalışma ekonomisi anlamında soydum hidroksit ile potasyum hidroksit arasında belirgin bir maliyet farkı mevcut olsa da potasyum hidroksit bazlı elektrolitlerin hücre voltajının sodyum hidroksitli elektrolitlerin hücre voltajına göre 0,5 ile 1,5 volt arasında daha az olması bu farkı kapatmaktadır.