YÜKSEK FOSFORLU ve AMONYUMSUZ RoHS UYUMLU AKIMSIZ NİKEL KAPLAMA
EKİPMANLAR:
Çözeltiye temas edecek tüm yüzeyler sıcaklığa ve aside karşı dayanıklı olmalıdır.
Tank | PVDF veya pigment içermeyen PP giydirilmiş tanklar veya anodik olarak (600-800 mV) korunan paslanmaz çelik tanklar kullanılabilir. Biri kaplama diğeri rezerv olmak üzere çift tank kullanılması önerilir. |
Isıtma | Anodik korumalı paslanmaz, porselen veya teflon ısıtıcılar kullanılabilir. Isı kaybının, aşırı buharlaşmanın ve kristalizasyonun önlenmesi için çalışma esnasında tankın yüzeyinin örtülmesi tavsiye edilir. |
Karıştırma | Hava hareketi önerilir. Borulama sistemi PP veya paslanmaz çelik olabilir. Delikler 2.5 mm çapında ve tankın alt yüzüne bakacak şekilde yanlara doğru olmalıdır. Sağlanan hava, kuru hava kompresöründen(Blower) sağlanmalıdır. Hava hareketi kaplanacak mallara direkt olarak çarpmamalı ve ısıtıcıların aşırı ısınması engellemek üzere ıstıcıların tam altında da bulunmalıdır. |
Havalandırma | Gereklidir. |
Filtrasyon | Tank hacmini saatte 8 -10 kez devredebilecek sürekli filtrasyon yapılmalıdır. (1 – 5 µm). Filtrasyon yatay değil dik pompa üzerinden çalışmalıdır. |
ÇALIŞMA ŞARTLARI:
Sıcaklık | 87oC (84 – 92 oC) |
pH | Elektrometrik 4.3 (4.3 – 4.8) |
Banyo Yükü | 1,5 dm2/l (0.5 – 2,4 dm2/L) |
Karıştırma | Askı ve/veya hava hareketi ; Banyonun her 1 m2 yüzeyi başına saatte 2.5-5 m3 hava verilmelidir. |
Banyo Ömrü | Çalışma şartlarına bağlı olarak, 42 – 48 g/l Nikel beslemesi yapıldığı zaman, yani 7 – 8 MTO sonunda banyonun tekrar kurulması gerekir. |
Kaplama Hızı | 10 μm/h (9 – 11 μm/h) |
AKIMSIZ NİKEL KAPLAMALAR ve ÖZELLİKLERİ
1. AKIMSIZ NİKEL KAPLAMALAR
Günümüzde endüstriyel uygulamalarda en yaygın olarak kullanılan katalitik kaplama işlemi, "Akımsız Nikel" kaplamadır. Bunun en önemli sebebi, akımsız nikel kaplamalarda ve prosesisin kendisinde bulunan benzersiz üstün özelliklerdir.
Birçok metal, uygun koşullar sağlandığında akımsız olarak kaplanabilir. Ancak akımsız nikel kaplama, çok yüksek sertlik, mükemmel aşınma ve korozyon direnci, düşük işçilik giderleri ve kolay uygulama özelliklerinden dolayı yaygın olarak kullanılmaktadır [1].
Akımsız nikel, özellikle son yıllarda artan sağlık ve çevresel kaynaklı kısıtlamalar nedeniyle, krom kaplamanın kaldırılmak istenmesi sonucu bir alternatif olarak, özelliklerinin ve görünümünün uygun olduğu pek çok uygulamada kullanılmaktadır. Bununla birlikte prosesin kimyasal kontrolünü ve özelliklerinin iyileştirilmesini sağlayan kurşun ve kadmiyum gibi katkıları içermeyen akımsız nikel çeşitleri de geliştirilmiştir [2]. Ayrıca PTFE, elmas ve seramik tozları gibi özellik geliştirici tanecikler eklenmesi ile elde edilen kompozit akımsız nikel kaplamalar ile ilgili birçok çalışma ve uygulama da bulunmaktadır. Tüm bunlar akımsız nikel kaplamaların uygulama alanlarını genişletmektedir.
1.1 Akımsız Nikel Kaplamaların Avantajları
Akımsız nikel kaplamayı avantajlı kılan özellikler arasında [3];
- Parçanın tüm yüzeyinde homojen kaplama sağlaması,
- Yüksek sertliği ve korozyona, aşınmaya ve aşındırmaya karşı yüksek dirençli olması,
- Lehimlenebilmesi,
- Düşük sürtünme katsayısı,
- Yüksek yansıma derecesi ve
- Manyetik özellikleri sıralanabilir.
1.2 Akımsız Nikel Kaplamaların Dezavantajları Akımsız nikel kaplamayı sınırlayan özellikler arasında [4];
- Akımlı yöntemlerle karşılaştırıldığında düşük kaplama hızı,
- Göreceli olarak yüksek kimyasal maliyeti,
- Gevrek kaplama elde edilmesi,
- Alüminyum alaşımlarına akımsız nikel kaplama uygulamadan önce önemli miktarda kurşun, kalay, kadmiyum ve çinko ihtiyacı bulunması sayılabilir.
1.3 Akımsız Nikel Kaplamaların Uygulama Alanları
Akımsız nikel kaplama yüksek korozyon ve aşınma direnci, yağlayıcılık ve lehimlenebilme özelliklerinden dolayı çok yaygın bir uygulama alanına sahiptir. Bu özellikleri sayesinde Tablo 1.1'de verilen endüstri uygulamalarında kullanılır.
Tablo 1.1: Akımsız Nikel Kaplamaların Uygulama Alanları [3]
Uygulama Alanları | Kaplama Parçası | Kaplama Kalınlığı (µm) |
Otomotiv | Motor yatakları, pistonlar, amortisörler, karbüratör parçaları, debriyaj balataları, egzoz manifoldları ve boruları, kilit parçaları, vites ve parçaları, jant kapakları, direksiyon parçaları ve milleri, hava yastığı donanımları, klima kompresörü parçaları, ABS parçalar | 2-40 |
Havacılık ve Uzay | Kompresör ve türbin kanatları, piston kafaları, motor ana mil ve çarkları, motor supapları, iniş takımları, jiroskop parçaları, flanşlar, ayna dişlileri, sürgüler, cıvatalar | 10-50 |
Kimya ve Petrol | Karıştırıcılar, vanalar, pompalar, reaksiyon tankları, kapaklar, yakıt boruları, nozüller, jigleler | 25-125 |
Elektrik ve Elektronik | Hafıza kartları, ısıtma tankları, alüminyum konektörler, diotlar, iç kilitler, bağlantı yerleri | 2-25 |
Diğer | Ameliyat araç ve gereçleri, ateşli silahlar, hidrolik silindirler ve miller, enjeksiyon kalıpları, dokuma tezgahları, baskı yatakları | 5-75 |
1. AKIMSIZ NİKEL KAPLAMA BANYO ÖZELLİKLERİ
Akımsız nikel kaplama prosesinde, nikel iyonları katalitik bir yüzey üzerine kimyasal olarak indirgenir ve kaplama meydana gelir. Kaplamanın kendisi indirgenme reaksiyonu için katalitik özelliktedir ve bu sayede çözelti içinde çözünen metal iyonları tükenene kadar bu reaksiyon devam etmektedir [3]. Bu oto katalitik indirgeme reaksiyonu sonucunda, kaplanan parçanın üzerine bileşimi ve kalınlığı her yerde aynı olan bir kaplama elde edilir. Elektrik akımı kullanılan kaplama proseslerinde bu durumdan söz etmek mümkün değildir.
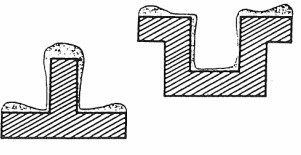
Şekil 2.1: Akımlı Kaplamalarda Kaplama Kalınlığı Dağılımı
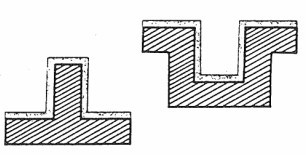
Şekil 2.2: Akımsız Kaplamalarda Kaplama Kalınlığı Dağılımı
1.1 Banyo Bileşenleri ve Görevleri
Akımsız nikel kaplama banyosunda her biri önemli görevleri yerine getiren farklı kimyasallar ve bileşenler bulunmaktadır. Bunlar:
- Nikel iyonları kaynağı olarak nikel tuzları,
- Nikeli indirgemek için elektron sağlayan indirgen madde,
- Banyonun ısıtılmasını sağlamak için enerji,
- Reaksiyonda kullanılan serbest nikelleri kontrol etmek için kompleks oluşturucular,
- Birikme esnasında meydana gelen pH değişimlerini düzenlemek için tampon kimyasal,
- Reaksiyon hızını arttırmaya yardımcı olan hızlandırıcılar ve
- Birikmenin sadece kaplanacak numune yüzeyinde ve tahmin edilen hızda olması için indirgeme reaksiyonunu kontrol eden dengeleyicilerdir.
2.1.1 Nikel İyonları Kaynağı
En çok tercih edilen nikel katyon kaynağı nikel sülfat olmasına rağmen, diğer nikel tuzları da bazı uygulamalarda kullanılır. Eğer kaplama korozyona karşı dirençli uygulamalarda kullanılacaksa nikel sülfat tercih edilir. Nikel sülfatla karşılaştırıldığında nikel asetat kullanımı banyo performansında ve birikinti kalitesinde önemli bir gelişme sağlamaz. Nikel asetatın kazandırdığı küçük avantaj fiyatının nikel sülfattan biraz daha az olmasıdır.
2.1.2 Enerji Kaynağı
Akımsız nikel kaplama çözeltisinin sıcaklığı, kaplama hızını etkileyen en önemli unsurlardan biridir. Kaplama banyosunda sıcaklık, enerji içeriğinin bir ölçüsüdür. 650C'nin üstündeki sıcaklıklarda birikme hızı yükselir. Bu durum çoğu sistem için geçerlidir. 100 0C sıcaklığın üzerinde ise akımsız nikel banyoları kararsız hale gelir. İşlem sıcaklığı 85–95 0C arasında tutulmalıdır [3].
2.1.3 İndirgen Maddeler
Akımsız nikel kaplama banyolarında sodyum hipofosfit, amin boron, borohidrür ve hidrazin gibi 4 farklı indirgen madde kullanılabilmektedir.
Akımsız nikel uygulamalarının çok büyük bir kısmında indirgen madde olarak sodyum hipofosfit kullanılmaktadır. Borohidrür ve hidrazine göre düşük maliyet, daha kolay kontrol edilebilmesi ve korozyona karşı daha dirençli kaplamalar elde edilebilmesi gibi avantajlar sağlar. Katalitik yüzeyin ve yeterli ısı enerjisinin varlığında hipofosfit iyonları, ortofosfite dönüşürler. Açığa çıkan hidrojenin bir kısmı katalizörün yüzeyindeki nikel iyonlarının indirgenmesini sağlar. Ancak ortamdaki hipofosfitin büyük bir kısmı, katalizör etkisiyle, ortofosfit ve hidrojen gazına yükseltgenir. Bu yüzden verim düşer ve ortalama % 37 verimlilikte 1 kg nikeli indirgemek için 5 kg sodyum hipofosfit gerekmektedir [3].
Akımsız nikel kaplama çözeltilerinde amin boron olarak, dimetilamin boron (DMAB) veya dietilamin boron (DEAB) kullanılmaktadır. DMAB suda çözülebilirken, DEAB kaplama banyosuna karıştırılmadan önce etanolde çözülür. Amin boron geniş pH aralığında etkili indirgen maddedir. Genellikle 6–9 pH aralığında kullanılırlar. Bu banyolar için çalışma sıcaklığı 50–800C arasındadır ancak daha düşük sıcaklıklarda da çalışır. Bu yüzden plastik, ametal gibi katalitik olmayan yüzeylerin kaplanmasında çok kullanışlıdır [5].
Sodyum borohidrür iyonu akımsız nikel uygulamaları için en güçlü indirgen maddedir. Nikel iyonlarının varlığında kendiliğinden nikel borür meydana gelir ancak çözeltinin pH'ı 12–14 arasında tutulursa bu oluşum önlenir ve reaksiyon sonucunda nikel elementi oluşur. 1 kg nikeli indirgemek için 0,6 kg sodyum borohidrür yeterlidir [5].
Hidrazinin indirgen madde olarak kullanıldığı banyolar 90–950C sıcaklık ve 10-11 pH aralığında çalışmaktadır. Daha yüksek sıcaklıklarda hidrazinin kararsızlığından dolayı bu banyoların kontrolleri zorlaşır [3]. Hidrazinin indirgediği çözeltilerde oluşan birikinti metalik görünüşe sahip değildir ve kırılgan bir yapıdadır. Bu yüzden günümüzde hidrazinin indirgediği akımsız nikel pek fazla uygulamaya sahip değildir [5].
2.1.4 Kompleks Oluşturucular
Akımsız nikel kaplama banyolarında kompleks oluşturucu madde olarak genellikle organik asitler veya tuzlar, inorganik pirofosfat anyonları ve amonyum iyonları kullanılır. Bu kompleks oluşturucu katkı maddelerinin kaplama hızını düşürmekle birlikte yerine getirdiği 3 temel görevi vardır [6].
- Nikel tuzlarının çökelmesini engellerler.
- Serbest nikel iyonlarının konsantrasyonunu azaltırlar.
- Tampon etkisi göstererek çözelti pH'ının çok hızlı düşmesine engel olurlar.
2.1.5 Hızlandırıcı Kimyasallar
Akımsız nikel banyolarına eklenen kompleks oluşturucuların, düşürdüğü kaplama hızının, kaplamayı çok verimsiz hale getirmemesi için kaplama çözeltisine düşük miktarlarda organik katkılar ilave edilir. Bu hızlandırıcı kimyasallar indirgen maddedeki hidrojenin kolayca ayrılmasını ve katalitik yüzey tarafından absorbe edilmesini sağlar [5]. Suksin asidi, karbonik asitler, çözülebilir florürler ve bazı solventler hızlandırıcı olarak kullanılabilir.
2.1.6 Dengeleyiciler
Akımsız nikel kaplama banyoları normal çalışma koşullarında dengeleyiciler eklenmeden uzun zaman çalışabilir ancak bir süre sonra kendiliğinden bozulabilir. Dengeleyici maddeler indirgeme reaksiyonunu kontrol eder ve birikmenin sadece kaplanacak parça yüzeyinde oluşmasına yardım eder. Bu kimyasallar tüm banyonun bozulmasını tetikleyen homojen reaksiyonları engellemek için de kullanılır. Dengeleyicilerin etkin bir şekilde kullanabilmesi için ilk olarak bu problemlerin dengeleyici kullanarak çözülebileceğini tespit edilmelidir. İkinci olarak, katalitik aktiflikte olumsuz kayıplardan kaçınmak için dengeleyicinin kullanılan işlemle uyumluluğu gözden geçirilmelidir. Üçüncü olarak iki veya daha çok dengeleyici kullanıldığında, bunlardan birinin diğer dengeleyicilerin etkisini azaltmadığından veya engel olmadığından emin olunmalıdır [6]. En çok kullanılan dengeleyicilerden biri kurşun tungstattır. Bu kimyasal birçok açıdan önemli üstün özelliklere sahip olduğu için tercih edilir.
2.2 İndirgenme Mekanizmaları
İndirgen madde olarak hipofosfit kullanıldığında meydana gelen kimyasal reaksiyon mekanizması için birçok teori öne sürülmüştür. Bunlar içerisinde en yaygın kabul edilen mekanizmalar aşağıdaki gösterilmiştir [7].
(H2PO2)- + H2O ısı+katalizör H+ + (HPO3)-2 + 2Hab | 2.1 |
Ni+2 + 2Hab Ni + 2H+ | 2.2 |
(H2PO2)- + Hab H2O + OH- + P | 2.3 |
(H2PO2)- + H2O H+ + (HPO3)-2 + H2 | 2.4 |
Yeterli ısı enerjisinin ve katalitik yüzeyin varlığında hipofosfit ((H2PO2)-) iyonları, ortofosfite ((HPO3)-2) dönüşürler. Açığa çıkan hidrojenin bir kısmı katalitik yüzey tarafından absorbe edilir (2.1). Katalizörün yüzeyinde bulunan Ni+2 iyonları, absorbe edilmiş aktif hidrojen tarafından indirgenir (2.2).
Böylece nikel kaplama oluşur. Aynı zamanda, absorbe edilmiş hidrojenin bir kısmı da, katalitik yüzeyde yer alan az miktardaki hipofosfiti, su, hidroksil iyonu ve fosfora indirger (2.3). Ayrıca ortamda bulunan hipofosfitin büyük bir kısmı, katalizör etkisiyle, ortofosfit ve hidrojen gazına yükseltgenir (2.4). Bu durum pH artışına ve kaplama veriminin düşmesine sebep olur.
Borohidrür iyonlarının asidik ve nötr çözeltilerde hidrolizi hızlıdır ve eğer ortamda nikel iyonları bulunuyorsa nikel borür kendiliğinden oluşur. Eğer kaplama çözeltisinin pH değeri 12 ve üzerinde tutulursa, banyonun bozulması engellenir. Böylece nikel ve borun alaşımı elde edilir. Bu birikme için kabul edilen reaksiyonlar aşağıdaki gibidir [7]:
BH - + 4Ni+2 + 8OH- 4Ni + BO - + 4H O | 2.5 |
Kaplamaya Etki Eden Faktörler2BH - + 4Ni+2 + 6OH- 2Ni B + H + 6H O | 2.6 |
2.3 Kaplamaya Etki Eden Faktörler
Akımsız nikel kaplama prosesini, banyonun bileşimi, pH değeri, sıcaklığı, yaşı, banyo yükleme faktörü ve karıştırma miktarı etkiler. Bunun yanı sıra indirgen maddenin konsantrasyon değişiminin, kaplama hızı üzerinde büyük etkisi vardır. İndirgen maddenin miktarı arttıkça kaplama hızı artar, ancak banyoda aşırısı bulunduğunda çözelti kütlesi içinde indirgenme oluşmasına neden olur. Bunun için uygun indirgen madde miktarı reaksiyon sırasında banyonun durumuna göre ayarlanmalıdır [3].
İndirgeme reaksiyonu sırasında hidrojen iyonları (H+) açığa çıkar. Bu durum banyonun pH değerini düşürür. Açığa çıkan hidrojen iyonunun miktarı, kullanılan indirgen madde türüne ve derişimine bağlıdır. Banyonun pH değeri, hem kaplama işleminde hem de birikintinin bileşiminde önemli bir etkiye sahiptir. Bu durum Şekil 2.3'de gösterilmiştir [5]. pH değeri arttıkça, kaplama hızı artarken, kaplama bileşimindeki fosfor miktarı azalmaktadır.
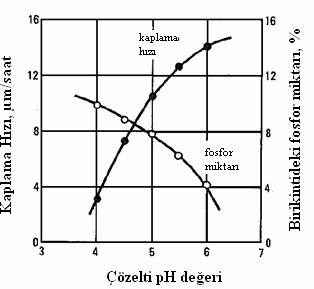
Şekil 2.3: Çözelti pH Değerinin Kaplama Hızı ve Birikintinin Fosfor İçeriğine Etkisi
Akımsız nikel kaplama çözeltisinin sıcaklığı 650C ve üzerinde olursa birikme hızı artar. Ancak 100 0C sıcaklığın üzerine çıkıldığında ise akımsız nikel banyoları kararsızlığa gider. Bu yüzden işlem sıcaklığı 85–95 0C arasında tutulmalıdır [3].
Banyo yaşı, çözeltideki nikel iyon miktarının tüketilme ve tekrar takviye edilmesi ile ilgilidir. Ortalama olarak bir akımsız nikel banyosu için en fazla 5-10 kere takviye tavsiye edilir. Banyo yaşlandıkça kaplama hızı düşer ve birikintinin özelliklerinde bir kötüleşme görülmeye başlar. Bu durumda banyo çözeltisi değiştirilmelidir [8].
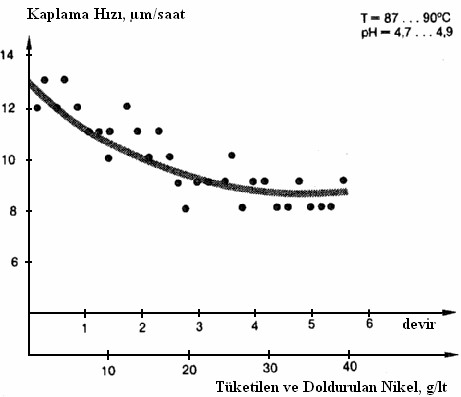
Şekil 2.4: Kaplama Hızının Banyo Yaşına Göre Değişimi [8]
Banyo yükleme faktörü, kaplama yapılacak parçanın yüzey alanının daldırıldığı tanktaki çözelti hacmine oranı olarak tanımlanır. Banyo yükleme faktörü arttığında, kaplama hızı da artar. Ancak kritik banyo yükleme faktörü üzerine çıkıldığı zaman banyo bozunabilir.
Akımsız nikel kaplama banyolarında karıştırma işlemi difüzyon hızını arttırdığı için gereklidir. Ayrıca banyonun daha homojen kalmasını sağlar. Özellikle karmaşık şekilli parçaların kaplanmasında mutlaka karıştırma yapılmalıdır [8].
3. AKIMSIZ NİKEL KAPLAMA TÜRLERİ
Akımsız nikel kaplamalar, kullanılan indirgen maddenin türüne göre fosfor ya da bor alaşımlı olarak elde edilir. Ayrıca çeşitli özellik iyileştirici katı taneciklerin eklenmesi ile kompozit akımsız kaplamalar üretilir.
3.1 Akımsız Nikel Fosfor Kaplama
İndirgen madde olarak hipofosfit kullanıldığı zaman, akımsız nikel kaplama, yapısında fosfor içerir. Bu kaplamalar düzgün yapılı, sert, göreceli olarak gevrek, doğal yağlayıcı özellikte, kolayca lehimlenebilir ve yüksek derecede korozyona dirençlidir. Isıl işlemler uygulanarak sertlik çok yüksek değerlere çıkarılabilir. Böylece ticari sert krom kaplamalara eşit veya daha yüksek aşınma direnci sağlanabilir [8].
Ticari akımsız nikel kaplamalar, banyo çözeltisinin içeriğine bağlı olarak, nikel matris içinde % 6–12 oranında fosfor ve yaklaşık % 0,25 oranında başka elementleri içerir. Bu kaplamalar kristal yapıya değil, amorf yapıya sahiptirler [7].
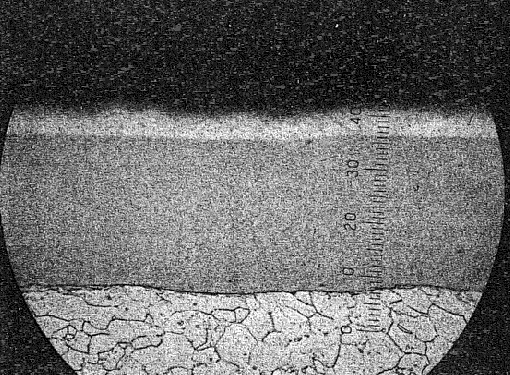
Şekil 3.1: 75 μm Kalınlıkta Akımsız Nikel Birikintisinin Kesiti (x400) [9]
Düşük fosfor içeriğine sahip akımsız nikel kaplamalar genellikle çatlaklı ve gözenekli yapıdadır. Bu durum birikintinin süneklik ve korozyon direnci özelliklerinin kötü olmasına neden olur. Akımsız nikel-fosfor kaplamaya, 220–260 0C'de ısıl işlem uygulandığında, yapısal değişimler oluşmaya başlar. 320 0C'nin üzerindeki sıcaklıklarda, birikinti amorf karakterini kaybedip kristalleşmeye başlar. Bu değişiklikler kaplamanın sertlik ve aşınma direncini iyileştirirken, korozyon direncinde ve sünekliğinde azalmaya neden olur [7].
Akımsız nikel kaplamalarda, çözeltiyle temas eden parçanın her bölgesinde kaplama bileşimi ve kaplama kalınlığı aynıdır. Parçanın dış yüzeylerinde olduğu gibi, oyuklar ve kör deliklerde de kaplama kalınlığı değişmez. Akımsız nikelin çoğu metale yapışması mükemmeldir. Katalitik metallerde oluşan başlangıçtaki yer değiştirme reaksiyonu, birikinti ile numune arasında metalik özellikle mekanik bağ kurulmasını sağlar [8]. İyi temizlenmiş çelik numunelerde yapışma kuvvetinin en az 300–400 MPa olduğu bulunmuştur. Paslanmaz çelik gibi katalitik olmayan veya pasif metallerde başlangıçta yer değiştirme reaksiyonu oluşmaz ve yapışma azalır (~140 MPa). Çoğunlukla uygun ön işlem ve aktivasyon ile kaplamanın yapışma kuvveti geliştirilir [6].
Akımsız nikel kaplamaların mekanik özellikleri diğer camsı metallere benzer. Çok yüksek dayanım, düşük süneklik ve yüksek elastiklik modülüne sahiptir. Bazı ticari kaplamalarda 700 MPa çekme dayanımına ulaşılır [9].
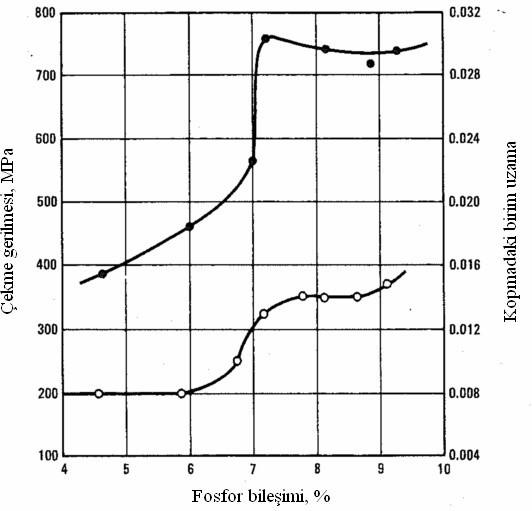
Şekil 3.2: Birikintinin Fosfor İçeriğinin Dayanım ve Kırılmadaki Birim Uzama Üzerine Etkisi [9]
Kaplama sonrası elde edilen mikrosertlik yaklaşık olarak 500 ile 600 HV100 arasındadır. Isıl işlemler bu alaşımların yaşlanmasına neden olur. Dayanım ve süneklik azalırken, sertlik yaklaşık 1200-1300 HV100 değerlerine çıkar ve ticari sert krom kaplamalardan daha sert kaplamalar elde edilir [8].
Akımsız nikel-fosfor kaplamaların yapısında porozite ve hatalar bulunmadığı takdirde, amorf yapısından ve pasifliğinden dolayı korozyon direnci mükemmeldir ve bu sayede saf nikel ve krom alaşımlarından daha iyidir [7].
3.2 Akımsız Nikel Bor Kaplama
Nikel-bor alaşımlı kaplamalar elde edebilmek için indirgen madde olarak borohidrür veya aminboron kullanılır. Bu kaplamaların özellikleri akımsız nikel-fosfor alaşımlarına benzemekle birlikte, sertliği oldukça yüksektir ve ısıl işlem uygulandığında sert kromun sertlik değerlerine ulaşılır. Aşınmaya karşı
dirençleri iyidir, ancak korozyon dirençleri daha düşüktür. Ayrıca, nikel-fosfor kaplamalara göre daha pahalıdır [7].
Akımsız Ni-B kaplamalarda bor miktarı yaklaşık olarak, aminboron çözeltileri için % 0,2-4, borohidrür çözeltileri içinse % 4-7 arasındadır. Borohidrürün indirgediği kaplamaların erime noktası 1080 0C iken, aminboronun indirgediği kaplamaların erime noktası yaklaşık 1350 0C'dir ve akımsız Ni-P kaplamalara göre oldukça yüksektir. % 5 B içeren Ni-B kaplamaların dayanım ve süneklik değerleri, yüksek fosforlu akımsız nikel kaplamalara göre oldukça düşüktür. Elastiklik modulü, kaplama sonrası 120 GPa iken, 400 0C' de 1 saat ısıl işlem sonrasında ise yaklaşık 180 GPa değerine çıkmaktadır [7].
Akımsız nikel-bor kaplamaların sağladığı en büyük avantaj yüksek sertlik ve aşınmaya karşı mükemmel dirençtir. Mikrosertlik değerleri 650 ile 750 HV100 arasında değişmektedir. 400 0C sıcaklıkta 1 saat ısıl işlem yapıldıktan sonra 1200 HV100 sertlik değeri sağlanabilmektedir. Daha düşük sıcaklık ve daha uzun süreli işlemlerde sertlik 2000 HV100 değerlerine kadar çıkarılabilmektedir. Isıl işlem sıcaklığının sertlik üzerindeki etkisi Şekil 3.3' de görülmektedir [9].
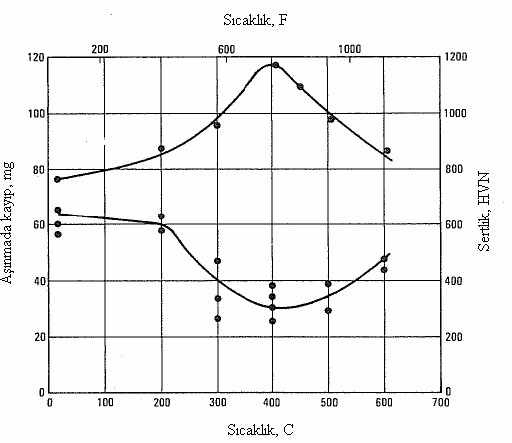
Şekil 3.3: 1saat Boyunca Farklı Sıcaklıklarda Yapılan Isıl İşlemin Akımsız Nikel-Bor Kaplamanın Sertlik ve Aşınma Direncine Etkisi
3.3 Akımsız Nikel Kompozit Kaplamalar
Akımsız nikel kompozit kaplamaların başlangıcı 1960'lı yıllara dayanmaktadır. Çözünmeyen parçacıkların, çözeltiye kaplamayla birlikte birikmek üzere eklenmesiyle elde edilirler [7]. Bu yüzden kaplamalarda geleneksel indirgeme reaksiyonu ile birlikte, özellik geliştiren parçacıkların süspansiyonu önem kazanır. Birlikte kaplamanın başarılı olması, parçacıkların katalitik kararlılığı, parçacık yükü, akımsız banyo bileşimi, banyo reaktivitesi, parçacıkların metal matrisiyle uyumu, kaplama oranı ve parçacık boyut dağılımı gibi çeşitli faktörlere bağlıdır. Banyo termodinamik olarak kararsız ve bozunmaya meyilli olmasına rağmen, küçük katı parçacık halindeki malzemeler akımsız kaplama banyosuna eklenir ve dağıtılır. Dağılmış parçacıklar dışarıdan filtre edilemezler [10].
Kompozit kaplamada kullanılan partikül maddeler, kazandırdıkları özelliklere göre değişiklik gösterirler. En çok kullanılan maddeler arasında, elmas, silisyum karbür, alüminyum oksit ve PTFE
tozları sayılabilir. Genellikle bu ince partikül maddelerin boyut aralığı 0,1-10 nm arasında seçilmektedir ve metal matrisindeki hacimce yüzdesi yaklaşık %40'tır [10]. Akımsız kaplamalara eklenmeleriyle birlikte, kaplamaların sertliklerini, aşınmaya karşı dirençlerini ve yağlama özelliklerini iyileştirirler.
Kaplamaların sertliklerini ve aşınmaya karşı dirençlerini iyileştirmek için kullanılan toz malzemeler arasında silisyum karbür (SiC), elmas, alüminyum oksit (Al2O3), krom karbür (CrC), titanyum karbür (TiC), bor karbür (B4C), veya tungsten karbür (WC) sayılabilir. Bu tozlar yaklaşık olarak 1–6 nm boyutundadır ve kaplama bileşiminin hacimce % 20–30'unu oluştururlar. Ticari uygulamalarda kaplama kalınlığı genelde 20-50 μm arasında tutulur [11].
PTFE katkıları kullanıldığı zaman, akımsız kompozit kaplamaların aşınma direnci ile birlikte, özellikle kuru yağlayıcılık ve ayrılma özelliklerinde iyileşme sağlanır. 0,5 nm çapındaki PTFE parçacıkları yüzey aktif maddeler ile ıslatılır ve akımsız nikel kaplama banyolarına belirli bir oranda eklenirler. Yağlamaya yönelik uygulamalarda genellikle 6-25 μm kalınlıkta kaplamalar yeterli olmaktadır. Bu kalınlıktaki kaplamalar aşınmaya dayanıklı kaplamalara göre daha incedir. Ancak gerektiğinde korozyona karşı direnç artışı sağlamak için bir alt tabaka olarak geleneksel akımsız nikel kaplama uygulanabilir [7].
4. SONUÇ ve ÖNERİLER
Endüstriyel uygulamaları ancak 1950'lerden sonra başlamış olan akımsız nikel kaplamaların başlıca üstün özelliklerini saymak gerekirse;
- Aşınmaya karşı mükemmel direnci ve ısıl işlem sayesinde çok yüksek sertliğe ulaşabilmesi,
- Yüzeyinde çok az gözenek içermesinden dolayı, çok yüksek korozyon direncine sahip olması,
- Düzgün olmayan yüzeylerde bile eş kalınlıkta ve aynı bileşimde kaplama elde edilebilmesi,
- Teorik olarak istenilen her kalınlıkta kaplama yapılabilmesi,
- Metal olmayan yüzeylerin bile belirli bir ön işlemden sonra rahatlıkla kaplanabilmesi,
- Dolap (tambur) ve askı kaplama uygulamalarına uygun olması,
- Kaplamanın oluşması için elektrik akımına ihtiyaç olmamasından dolayı, pahalı akım kaynakları ve askı sistemleri gerektirmemesi sıralanabilir.
Akımsız nikel kaplama uygulamaları, günümüz endüstrisinde çokça kullanılıyor olsa da, kompozit kaplamalar hala başlangıç aşamasında sayılabilir. Bununla birlikte yapılan araştırma ve çalışmalar hem kullanıcı hem de tasarımcılar tarafından takip edilmelidir. Kompozit kaplamaların vaat ettiği geliştirilmiş sertlik, aşınma direnci ve yağlayıcı özellikleri, aşınma uygulamalarında kullanılan sert krom uygulamalarına alternatif olmasını sağlar. Böylece kromun yarattığı sağlık ve çevresel sorunların da önüne geçmek mümkün olacaktır.