KAPLAMA TESİSLERİNDE DURULAMA TEKNİKLERİ, DURULAMA EKONOMİSİ ve DURULAMANIN MATEMATİĞİ
TANIM :
Kaplama tesislerinde, hem birim maliyetleri, hem de kaplama kalitesini belirleyen en önemli işlemlerden biri de durulamalardır. Bu tesislerde etkin bir durulama teknolojisinin kullanılması, temiz su kaynaklarının giderek tükendiği dünyamızda, -maliyetler ve kalite dışında- çevre duyarlılığı bakımından da büyük önem taşımaktadır.
Sonuçta durulama işlemi, zararsız su filminin zararlı proses çözeltisi filmiyle yer değiştirmesi suretiyle parça üzerine bulaşmış zararlı filmin uzaklaştırılmasıdır. Yüksek kalitede kaplama yapmak ancak temiz katodun, saflığı kontrol edilen elektrolit içerisinde kaplanmasıyla mümkündür. Kalitesiz ve yetersiz durulama işlemleri, proses içindeki her ardışık basamağın birbirini bozmasına neden olur. Kaplamanın lekelenmesine, noktacık oluşumuna, kabarma ya da soyulmalara ve kirli çözeltilere neden olur. Düzgün hazırlanmış, çoklu ters-akışlı durulama sistemi su sarfiyatını azaltıcı yönde etkilediği gibi çalışma ve atık su maliyetinin de düşmesini sağlar.
Durulama, bir bakımdan da aslında bir çeşit sulandırma işlemidir. Parça yüzeyindeki kimyasalların etkilerinin minimum oldukları noktaya kadar sulandırılması, böylelikle çözeltilerin zaman içerisinde kirlenmesinin engellenmesi esasına dayanır. Çoklu ters-akışlı durulama sisteminin tasarlanması ve uygulanması, minimum miktarda su kullanımıyla etkili bir durulamanın yapılabilmesine olanak sağlar.
Genel olarak parçanın çeşitli işlem basamakları arasında direkt olarak yıkanması gereklidir. Örneğin, alkali temizleme çözeltisinden taşınan yıkanmamış film, yıkanmadan götürüldüğünde sonraki dekapaj asitini kirletir. Böylelikle bir sonraki kaplama banyosu da kirlenir. Aşırı kirlenmiş durulama çözeltileri parçanın yüzeyinin pasiflenmesine neden olduğu gibi, parça yüzeyinde tepkime ürünü çökeltilerinin de oluşmasına neden olur. Eğer en son proses işleminin durulama suyu yeterince temiz değilse, parçanın kötü görünmesini sağlayacak, aşındırmaya ya da başka bir zararlı etkiye neden olabilecek tuz noktaları oluşur. Böylelikle parça üzerindeki bulaşık film tabakasının sulandırılmasıyla, tuz lekeleri ve takip eden proses basamaklarının temiz kalması sağlanabilir.
DURULAMA TEORİSİ
Durulama sularındaki genel gerekli seyrelme oranlarıyla ilgili tavsiyeler literatürlerde bulunabilir. Çok genel kural olarak 1/1000 seyreltme oranı çoğu durum için iyi bir başlangıç noktasıdır. Durulama sularındaki kirlilik konsantrasyonunun belirlenmesi önemlidir. Çünkü bu durulama işleminin etkinliğinin göstergesidir. Yıkanmış parça tanktan bu çözelti üzerindeyken ayrılır ve durulama suyu atık su hattına bu kompozisyonda gider.
Çeşitli kaynaklar, durulama tankında oluşan kirliliği belirlemek için bazı eşitlikler önermişlerdir. Her durumda, durulama suyu ve taşınan suyun tamamiyle ve hemen karıştığı varsayılmalıdır. Pratikte uygulandığı zaman aşağıdaki parametrelere dikkat edilmesi suretiyle yakın sonuçlar elde edilebilir.
- Durulama tankına sağlanana hava yardımıyla kuvvetli karıştırma.
- Temiz suyun tankın dibinden sağlanması.
- Pis su giderinin temiz su beslemesinin ters yönünde olacak şekilde konumlandırılması.
Çeşitli durulama işlemlerini açıklayıcı başlıca eşitlikler aşağıdaki terminoloji kullanılarak verilmiştir;
V: Durulama tankının hacmi, l
Q: Durulama tankına sağlanan temiz suyun akış oranı, lpm M: Durulama işlemleri arası geçen süre, dk
D: Her durulama işleminde parça ya da askı üzerinde taşına suyun hacmi, l n: t sürede yapılan durulama işlemi sayısı,
C0: Taşınacak kirli suyun kirlilik konsantrasyonu, g/l
Ct: t süre sonra durulama tankındaki kirliliğin konsantrasyonu, g/l Ce: Durulama tankındaki kirliliğin denge konsantrasyonu, g/l
Cr: Seri durulamalardan son durulamadaki kirliliğin denge konsantrasyonu, g/l S: Spreylerde kullanılan suyun ortalama oranı,
Durum I: Temiz su beslemesi yapılmayan durulama tankına taşınma (veya proses tankına)
Ce = C0 (1)
Ct = C0 {1-[V / (V + D)]n} (2)
Durum II: Temiz su beslemesi yapılan tanka taşınma
Ce = [D / (QM + D)] . C0 (3)
Ct = Ce { 1- [(V - D)/(V + D)]n e-Qt/V} (4)
Durum III: Seri durulamalar. Ayrı ayrı temiz su beslemesi olan r adet durulama var; (Q1 , Q2 , , Qr)
Cr = [ D / (Q1M + D)] . [ D / (Q2M + D)9 . ... . [ D / (QrM + D)9 . C0 (5)
Durum III(a): Durum III le aynı fakat her tank aynı su beslemesiyle besleniyor (Q)
Cr = 8 D / (QM + D)] . C0 (5a)
Durum IV: Çoklu birbirine bağlı geri akışlı durulamalar. r'nci durulama Q basınçlı temiz suyla besleniyor
QM / D = Y (Y > 1)
Sonra
Cr = [ (Y - 1) / (Y(r+1) – 1)] . C0 (6)
Veya alternatif olarak,
Cr = [1 / (1 + Y + Y2 + ..... + Yr) ] . C0 (6a)
Durum V: Spreyli tek, temiz su beslemeli durulama
Ce = [ D / (M(Q + S) + D)] . C0 (7)
Bu artan eşitliğin eğrisi şekil 1' de gösterilmiştir: Z = 1 – e-F
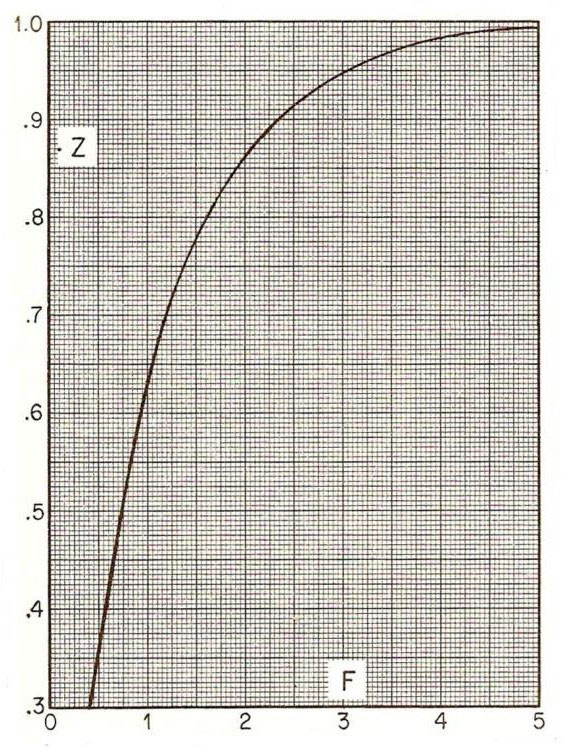
Şekil 1. Z = 1 – e-F'nin artan eğrisi.
- Su beslmesiz durulamalar için;
F = nD/V ve Z = Ct/C0
- Su beslemeli durulamalar için; F = Qt/V ve Z = Ct/Ce
Bu eğri tek durulamalı sistemlerde, (2) ve (4) numaralı eşitliklerin n durulamadan sonraki anlık konsantrasyonlarının(yani t'nci dk'daki) sunumu için kullanılabilir.
Taze su beslemesi olmayan sistemlerde, eğer nD/V değeri F olarak absiste kullanılırsa; Z, Ct/C0 değerini verir. Benzer şekilde, tek banyolu taze su beslemeli durulamalar için, F olarak Qt/V değeri kullanılırsa; Z, Ct/Ce'nin yaklaşık değerini, yani, ulaşılan denge konsantrasyonunun kesrini verir. Ters işlemle, şekil 1, verilen durulamadaki denge konsantrasyonunun kesrinin yaklaşık oluşma zamanını hesaplamada kullanılabilir. Örneğin, eşitliğin %95ini oluşturan Qt/V değeri 3'e tekabül etmektedir. Diğer bir ifadeyle, durulama tankı, hacminin 3 misli su ile beslendiği zaman, konsantrasyon dengenin %95'i olacaktır. Qt/V değeri 5 olduğu zaman denge(%95i geçmiş olacak) büyük ölçüde tamamlanmış olacaktır. Pratik olarak anlatmak gerekirse, 200 l'lik durulama tankı 2 lpm su ile beslendiğinde %95'lik dengeye
Şekil 2 eşitlik (3), (5a) ve (6)'nın grafiksel gösterimidir. Çoklu durulamalar için, eğriler, her durulamadaki besleme hızının eşit ve Q'nun toplam besleme olduğu durumlar için çizilmiştir. Eğer böyle yapılmıyorsa, 2 ve 4 eğrileri veya 3 ve 5 eğrileri ayırdedilemez. Durum 5'te açıklanan spreyle durulamaya gelince, eşitlik 7 tanktaki denge5saatte ulaşacaktır.
konsantrasyonunu verir, bu, parça spreyden ayrıldıktan sonra üzerinde kalan sıvının konsantrasyonundan daha büyüktür. Çünkü bu işlem aslında basamaklı durulamadır. Sprey durulamasıyla ne mertebede sulandırma sağlandığını hesaplamak mümkün değildir, ancak pratik çalışmalar için kaynaklar, parçanın kapalı bölümleri dışında kalan bölümler için, normalden bir buçuk kat daha fazla sulandırdığını varsaymaktadır.
DURULAMA DENGESİ
Bir kompleks olayın anlaşılması için en iyi yaklaşım, öncelikle bütün sistemi en başından değerlendirmektir. Bir boş tank düşünelim. Daha sonra bu tanka 1 birim konsantre kaplama çözeltisi ve 999 birim su ilave edip iyice karıştıralım. Oluşan toplam 1000 birim çözelti, 1 birim kaplama çözeltisi içerecek ya da % 0.1 konsantrasyonunda olacaktır.
Bizim durulama olayını anlamamızdaki sonraki adım, denge prosesi olarak neyin bilindiğini kapsar. 1000 birim % 0.1'lik çözeltiyi ele alarak başlayalım, ancak bu çözeltiyi kendi başına bırakmak yerine, karışım tankı taşana kadar 1: 999 oranında kaplama çözeltisi ve su ilavesi yapalım. Çok detaylı düşünmeden aslında içerdeki şeylerin dengede olduğunun farkına varabiliriz. Tankın içinde konsantrasyonu % 0.1 olan çözelti var, tanka % 0.1 konsantrasyonunda çözelti giriyor ve tanktan taşan sıvının konsantrasyonu da % 0.1.
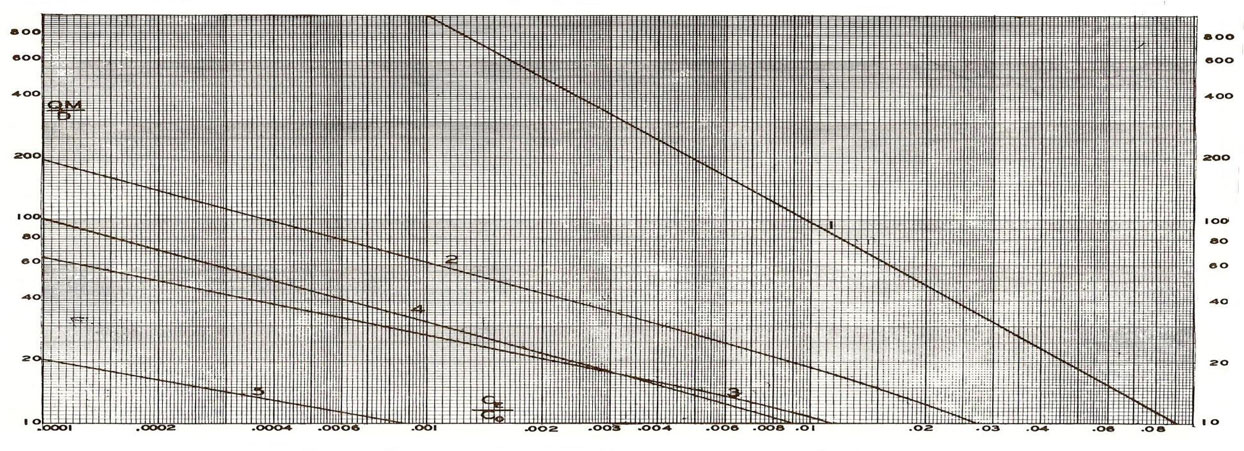
Şekil 2. Su beslemeli durulamalarda teorik denge Eğri 1. Tek Durulama
Eğri 2. Eşit, ayrı su beslemeli ikili durulama Eğri 3. Eşit ,ayrı su beslemeli üçlü durulama
Eğri 4. Su beslemesi ikinci durulamaya yapılan ikili tes-akışlı durulama Eğri 5. Su beslemesi üçüncü durulamaya yapılan üçlü ters-akışlı durulama
Şimdi bu sürekli taşmanın olduğu bu işleme yıllar önce başladığımızı ve şimdiye dek devam ettiğimizi düşünelim. Bu taşkanlı sistemdeki durulama suyunun konsantrasyonun % 0.1 olduğundan eminiz. Şimdi şöyle bir durumla karşılaştığımızı varsayalım. Yıllar önce deneye başlarken 1 birim kaplama çözeltisinin eklenmesi unutılmuş ve böylelikle deneye 1000 birim suyla başlamışız. Sezilerimiz bize taşkandan taşan sıvının konsantrasyonunun yıllar önceki deneye başlama şartlarından etkilenmiş olamayacağını söyler ve bu doğrudur. Sistem yıllar önce dengeye yakın, farkın ölçülemeyeceği bir hale dönüşmüştür. Bu, proses dengeye ulaştı dediğimiz durumdur. Tankın, arzulandığı gibi 1: 999 ‘luk karışım veya saf su, ya da doğrudan kaplama çözeltisiyle dolu olmasının önemi yoktur. Eğer tankın içine, yeterli periyotlarla 1 birim kaplama çözeltisi ve 999 birim su ilave etseydik tankın konsantrasyonu ilk durum ne olursa olsun 1 birime 999 birim olurdu. Bu çoğu durulama uygulamalarının gerçek durumudur.
İÇERİ GİREN TUZ = İÇERİDEN ÇIKAN TUZ
Mohler basitçe durulama tankındaki denge şartlarını mantığı tartışılamayacak bir ifadeyle açıklamıştır : İçeri giren tuz = İçeriden çıkan tuz
Durulama tankının içine giren tuz , proses tankından çıkan parça üzerine yapışan çözelti tarafından gelir. Buna genellikle içeri taşınma denir. Durulama tankı içinden çıkan tuz ise genel olarak taşan durulama suyudur. Bir miktar tuz da dışarı taşınmayla durulama suyunda çözünerek tankı terk eder ancak bu küçük bileşendir. Şekil 3 dengedeki bir durulama tankını göstermektedir.
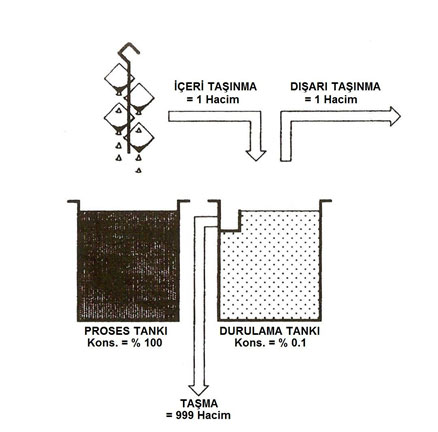
Şekil 3. Tek basamaklı Durulama
Eğer durulama tankında iyi bir karıştırma olduğunu varsayarsak, durulama tankının konsantrasyonunu istenen değerde tutmak için gerekli taşma oranını belirleyebiliriz. Örneğin saatte taşınmanın 1 hacim kaplama çözeltisi olduğunu biliyorsak, ve durulama tankının kabul edilebilir konsantrasyonu % 0.1'se gerekli taşma oranını aşağıdaki gibi hesaplayabiliriz
İçeri giren tuz = 1 hacim içeri taşınma x %100 kons. = 1 birim tuz İçeriden çıkan tuz = İçeri giren tuz = 1 birim tuz
= dışarı çıkan hacim x % 0.1 izin verilen kons.
Dışarı çıkan hacim = 1 birim tuz / % 0.1 kons. = 1000 hacim
Gerekli taşma oranı = 1000 hacim – dışarı taşınma hacmi = 999 hacim
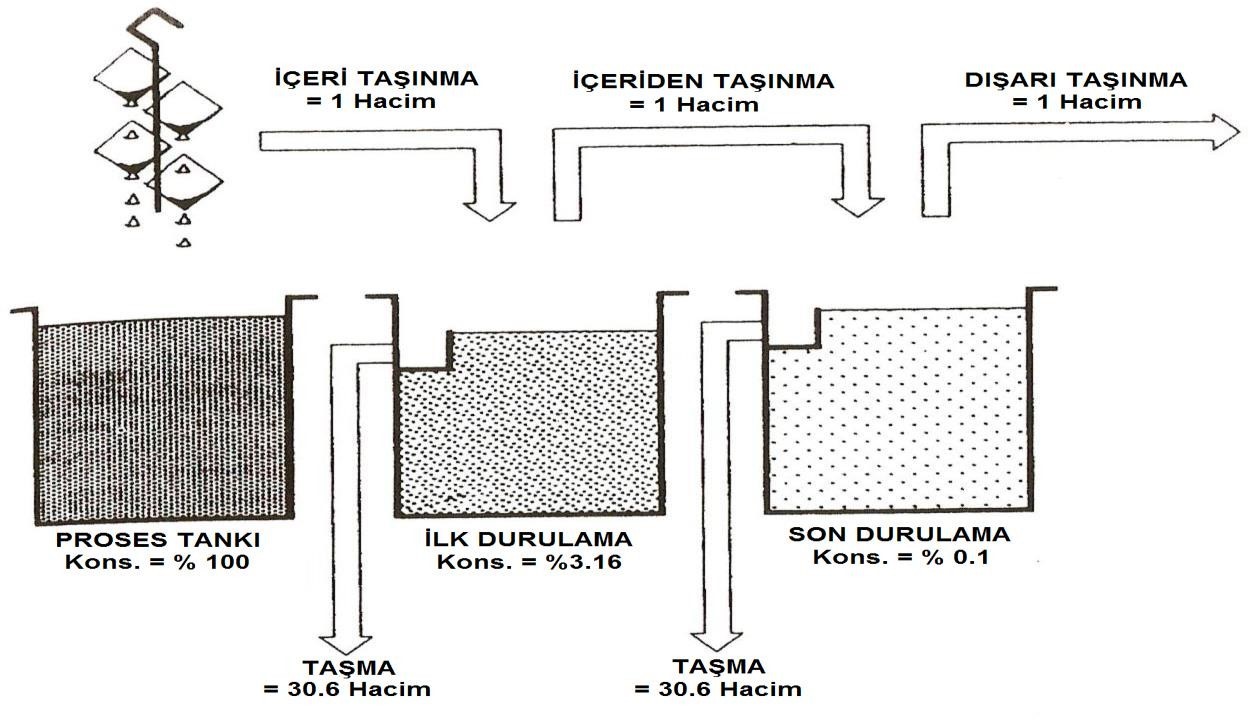
Şekil 4. Çift Basamaklı Durulama
Şekil 4 aynı problemi iki banyo kullanılan sistemler için göstermektedir. Taşma oranı, son durulamada aynı % 0.1'lik konsantrasyonu sağlamak için tank başına 30.6 hacim veya toplamda 61.2 hacim olmalıdır. Her durulama tankı için toplam tankı terk eden durulama suyu 31.6 hacim(30.6 hacim taşma+1 dışarı taşınma)dır. 31.6 değerinin rastlantısal
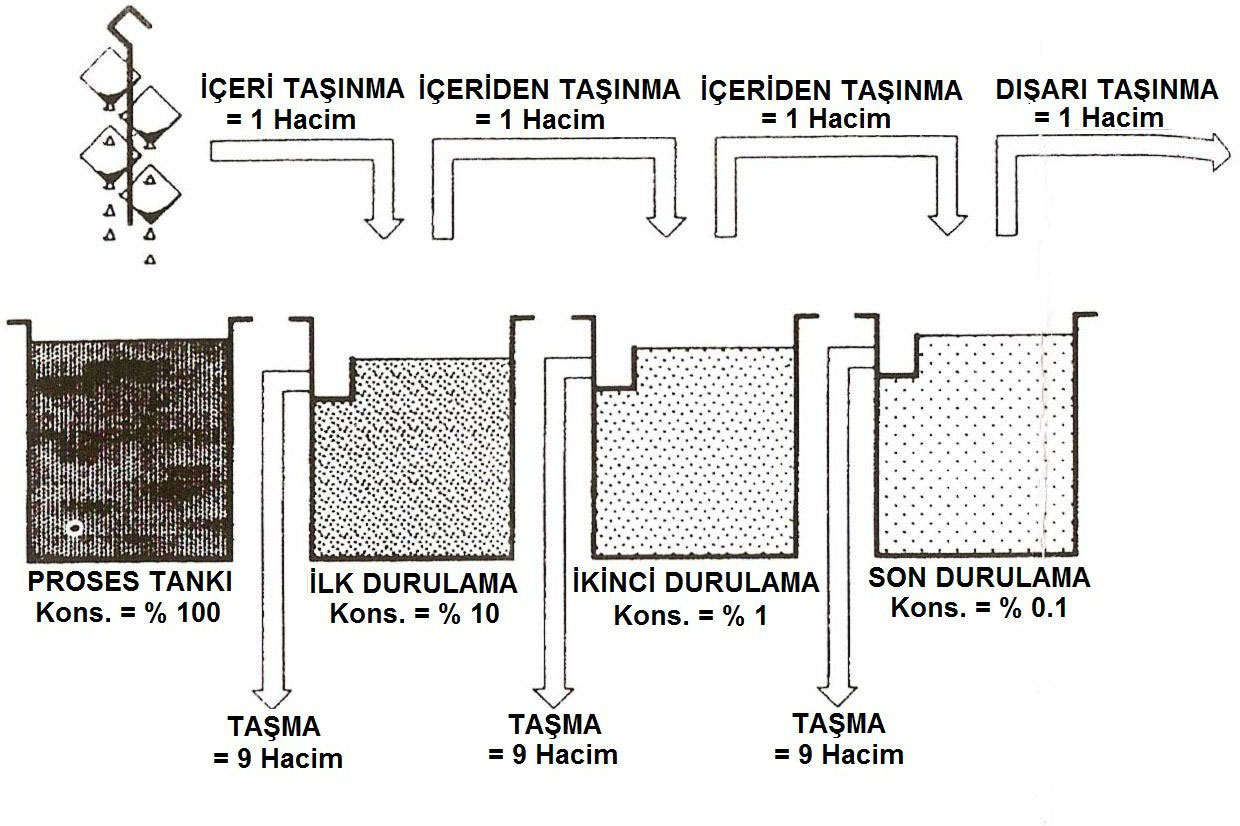
Şekil 5. Üç Basmaklı Durulama
olarak 1000'in karekökü olmadığına dikkat ediniz. Eğer proses tankının konsantrasyonu ilk durulama konsantrasyonunun 31.6 katıysa, ve ilk durulamanın konsantrasyonu son durulamanın konsantrasyonunun 31.6 katıysa, son durulamanın konsantrasyonu proses tankının konsantrasyonunun 1/1000'i kadardır.
Eğer amaç son durulamanın konsantrasyonunu istenen değere en az durulama suyu sarfiyatıyla düşürmekse, suyu dağıtmanın en uygun yolu, her iki banyoya da eşit şekilde dağıtmaktır. Fakat hatırlanmalıdır ki, bizim iddiamız asıl amacımızın bu olmadığıdır.
Şekil 5'te gösterildiği gibi üçüncü bir durulama eklenmesi durumunda, istenilen taşma oranı tank başına 9 hacme düşmektedir(tank başına tanktan ayrılan su 10 hacim yani 1000'in küp kökü). Eğer dördüncü bir durulama kullanılırsa, istenen taşma oranı tank başına 4.6 hacimdir. Bu yüzden, kurutma öncesi son durulama gibi, yüksek sulandırmanın istendiği durumlarda çoklu durulama kullanmak daha karlıdır. Minimum durulamanın kabul edilebildiği, sıcak yağ alma ve elektrikli yağ alma arası durulama gibi durumlarda ise iki durulama kullanmak zordur.
TERS AKIŞLI DURULAMA
Şekil 6'de teknik olarak ters-akışlı durulama olarak adlandırılan, son durulama suyunun taşkanının önceki durulamanın beslemesi olarak kullanıldığı durulama metodu gösterilmektedir. Aynı durulama suyunun iki sefer kullanılmasından dolayı, gerekli su miktarı, iki durulamalı normal bi sistemle karşılaştırıldığında, toplamda 31.1 hacme, neredeyse yarısına düşmektedir.
Ters-akışlı sistem için aynı formülleri çözmek biraz daha karışıktır. Çünkü son durulamadan önceki durulamaya beslenen su bir miktar tuz ihtiva etmektedir.
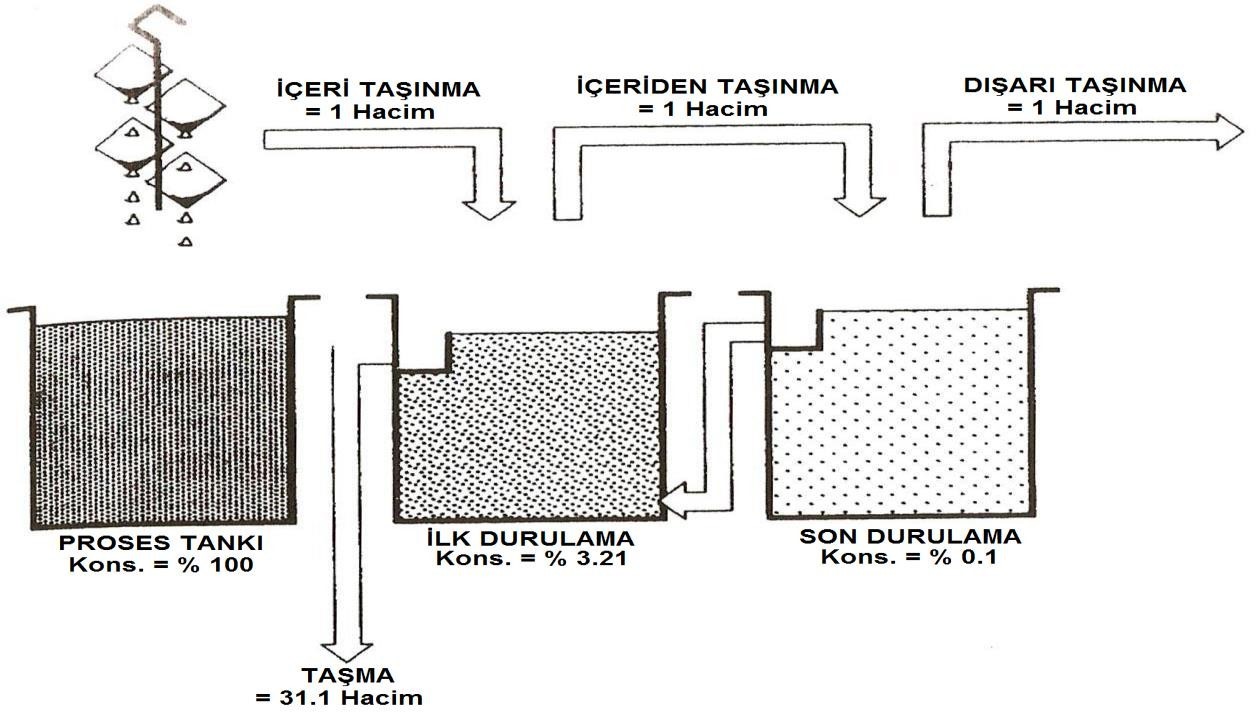
Şekil 6. Ters-Akışlı Durulama
İlk durulamaya bakılırsa:
İçeri giren tuz = 1 hacim içeri taşınma x %100 kons.+ ters-akış hacmi x son durulama kons. İçeriden çıkan tuz = (1 hacim içeriden taşınma + taşma hacmi) x ilk durulama kons.
Son durulamaya bakılırsa:
İçeri giren tuz = 1 hacim içeriden taşınma x ilk durulama kons.
İçeriden çıkan tuz = (1 hacim dışarı taşınma + ters-akış hacmi) x son durulama kons.
Bundan dolayı her durulamanın konsantrasyonu diğerlerine bağlıdır. Yukarıdaki denklemleri çözmenin geleneksel yolu çeşitli matematiksel teknikleri kullanmaktır. Ancak günümüzde kolaylıkla erişilebilen bilgisayarlar karışık matematiksel tekniklerle uğraşmadan yukarıdaki denklemlerin sonuçlarını verebilmektedir.
Verdiğimiz sonuçların teorik olarak bulunduğuna dikkat ediniz. Prtaikte ters-akışlı durulamalar iş yoğunluğu sebebiyle önceki durulamanın çok kirlenmesi ve son durulamaya kirli su taşıması sebebiyle gerektiği gibi kullanılamamaktadır. Teorik modelle aynı olmasını sağlamak için borulamanın yeterince büyük ve havasız olmasına ve sifon etkisinin yeterli olmasına dikkat edilmesi gerekmektedir.
Ters-akışlı durulamanın istendiği, ancak gerekli sifon etkisinin olmadığı durumlarda, durulama suyu bir tanktan ötekine, air lift (hava kaldıracı) olarak adlandırılan ve çok havalandırılmış suyun aynı hacimdeki normal sudan daha hafif olması prensibine göre çalışan basit bir düzenek yardımıyla alınabilir.
Alan yetersizliği ya da ürün gerçeklerinin diğer bir durulamayı ilave etmeyi engellediği durumlarda, ikinci bir durulama yerine durulama tankı üzerine sprey başlıkları yerleştirilebilir. Ters-akış prensiplerine göre taze su beslemesi sadece son durulamaya yapılır, spreyler sadece parçalar tanktan çıkarken aktif hale geçer.
DURULAMA KRİTERİ (ÖLÇÜTÜ)
Ce/C0 (veya çoklu durulamada Cr/C0) durulamayla elde edilen sulandırma derecesini ifade eder. Bu çift taraflı kesir durulama kalitesini belirleyen elverişli bir kriterdir (yani 1/1000 konsantrasyonunda bir durulama suyu 1/500 konsantrasyonundaki durulama suyundan daha iyi durulama sağlar). Bu dengelerin birbirleriyle eşitlenmesi sonucu elde edilebilir, her durumda C0/Cr, (QM/D)r ye % 1 hata ile eşitlenebilirken, sık olan durum QM/D %100 eşitlenebilir. Bu durulama kurulumlarını hesaplamak ve tasarlamak için hızlı ve elverişli bir yoldur.
TAŞINMA
D Taşınma hacminin önemi, yukarıdaki eşitliklerde görülmektedir. Parça yüzeyinden kaynaklı çözelti taşınmasının azaltılması için genel kurallar şöyle sıralanabilir :
- Parçanın yere göre mümkün olduğunca dikey asılması
- Parçanın daha uzun kenarının yatay olarak askılanması
- Parçanın en alt kenarı yere göre eğik ve son damla kenar yerine köşeden akacak pozisyonda askılanması
- Parçanın çözeltiden yavaşça çıkarılması
- Parçanın banyo üzerinde bir-iki dakika ya da üzerindeki çözeltinin damlaması bitene kadar süzülmesi
Özellikle otomatik sistemlerde, tanktan tanka parça transferleri süzülme zamanından daha kısa süre içerisinde yapılabilmektedir. Ancak yine otomatik sistemlerde, parçanın çözelti içerisinden alınmasının yavaşlığının ayarlanabilmesi halinde, hızlı bir transfere rağmen daha az taşınma olacaktır.
Tablo I'de çeşitli sınıflarda parçalar için, Soderberg tarafından belirlenen taşınmalar gösterilmiştir. Bu bilgiler durulama hesaplarının yapılması veya beklenen çözelti kayıplarının tahmin edilmesi ve atık su sistemine uygun ilavelerin yapılması için kullanışlıdır.
Parça Sınıfı | Taşınma (l/1000 dm2) |
Dik parça, iyi süzülmüş | 0,16 |
Dik parça, zayıf süzülmüş | 0,81 |
Dik parça, çok zayıf süzülmüş | 1,62 |
Yatay parça, iyi süzülmüş | 0,32 |
Yatay parça, çok zayıf süzülmüş | 4,07 |
Çukurlu parça, çok zayıf süzülmüş | 3,25-9,77 veya daha fazla |
Tablo 1.Birim alan başına taşınma
Soderberg'in çalışmaları üzerinde yapılan tartışmalar, kaplama ya da temizleme çözeltilerinin viskozitelerinin taşınma hacmi üzerinde çok büyük bir etkisinin olmadığını göstermiştir.
Sıcak çözeltilerden taşınma daha az olmakta, düşük yüzey gerilimi ise taşınma hacminde önemsiz bir azalmaya neden olmaktadır.Sıcak ve soğuk çekilmiş demirin çözelti taşımaları karşılaştırıldığında, yüzey pürüzlülüğünden kaynaklı herhengi bir etki bulunamamıştır.
Kushner, taşınma hacmi kontrolünü, parçaların çözelti içinden çıkarılması ve süzülmesi olarak iki evrede göz önüne almıştır. Öncelikle dik asılan parçanın üzerinde kalan çözelti miktarı parçanın çözelti içersinden çıkarılma hızı ve çözeltinin kinematik viskozitesinin karekök ürünüdür. Yüzeysel analizler ve Soderberg'in deneysel çalışmalarından, Kushner, parça üzerinde kalan çözelti filmi kalınlığı, f için aşağıdaki ifadeyi ortaya çıkarmıştır:
F=0,02√UV (8)
U ve V c.g.s. sistemine göre hız ve viskozitedir. Kushner aynı zamanda Soderberg'in belirttiği taşınmanın sıcak çözeltilerde düşmesini, viskozitesinin düşmesine bağlamıştır.
Eşitlik (8) bu şekilde de yazılabilir;
W = 0,02A√ap/td (8a)
Bu eşitlikte W; parça üzerindeki sıvı hacmi(cm3), A; parçanın alanı(cm2), a; parçanın yere göre dik uzunluğu (cm), p; sıvının viskozitesi(poise), t; süre(saniye), ve d; çözeltinin yoğunluğudur.Soderberg'in beş eşitliğinden ilk dördü yukarıdaki eşitliten çıkarılabilir.
Film kalınlığının düştüğü, süzülme zamanı, eşitlik (8a)'daki değişkenlere, yüzey geriliminin eklenmesiyle kontrol edilebilir. Birim alan başına akan sıvı miktarı, çözelti yoğunluğunun ve süzülme zamanının arttırılması ve aynı şekilde parçanın yere göre dik uzunluğunun ve çözeltinin viskozitesi ve yüzey geriliminin düşürülmesiyle artar. Böylece her iki evre için tüm bilinen faktörler göz önüne alınarak, taşınma önemsiz hale getirilir.
TANK HACMİNİN ETKİSİ
(1) - (7) eşitlikleri arasında da görülebileceği gibi teorik olarak tank hacmi yalnızca denge konumuna ne kadar zamanda erişileceğini hesaplamada kullanılırken, ortalama denge konsantrasyonuna herhangi bir etkisi yoktur. Geçmişte bu konuyla ilgili çok tartışmalar yaşanmıştır. Ancak pratik uygulamalar göstermektedir ki büyük durulama tankına para harcamak yerine başka yerlere harcamak daha iyidir. Ayrıca daha küçük durulama tankına kuvvetli hareket koymak daha kolaydır.
Etkili çalışabilmeleri için durulama tanklarının tasarımı önemlidir. Taşkan, döngünün sağlıklı olabilmesi için uzun olmalıdır. Akış taşkanının olmaması beslenen suyun tankın tamamında değilde sadece bir bölümünde etkili olmasına neden olur. Bu, taşan suyun konsantrasyonunun tankın konsantrasyonundan daha düşük olmasına yani suyun boşa harcanmasına neden olur.
Sıralı delikler açılmış bir borunun tankın dibine yerleştirilmesi ve su beslemesinin buradan yapılması karıştırma etkinliğini arttırmak açısından önemlidir.
Daha öncede bahsedildiği gibi, ters-akışlı durulamada sifon etkisinin yeterli olması ve tasarının uygun olarak yapılması önceki durulamadan son durulamaya kirli suyun taşınmasını engellemek açısından oldukça önemlidir.
HAREKET ETKİSİ
Daha önce bahsedildiği gibi durulama bir sulandırma işlemidir, ve eğer bu işlem durulama tankındaki tüm suyla yapılırsa etkilidir. Durulama teorileriyle ilgili tüm hesaplamalar bu varsayıma dayanılarak yapılır. Karıştırma yetersiz ise, tank içine verilen taze su kısa bir süre için tankta kalır ve tankın konsantrasyonu ve taşınma kayıpları belirsizce artar. Bu durum, hava hareketinin -parçaların tanktan uygusuz çıkarılması ve uygunsuz sıçramalar engellendiğinde-, iyi bir yöntem olmasının nedenini açıklar. Hava hareketinin durulama tankına uygulanma yöntemi kaplama banyolarına uygulanma yöntemiyle aynı olmasına karşın, uygulanan havanın basıncı kaplama banyosuna uygulanandan biraz daha fazladır. Taze
hava banyoya, sprey kullanılmayan banyolar için, daima banyonun tabanından sağlanmalıdır. Hava banyoya, banyodaki döngüye uygun ve tankın üst kısmında temiz durulama suyu bulunmasını sağlayacak şekilde bağlanmalı, yağsız olmalı ve düşük basınçlı blowerla sağlanmalıdır.
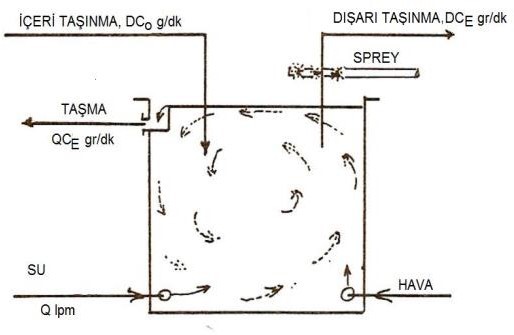
Şekil 7. Durulamada ideal karıştırma
Tankın uç kısmında taşkan bulunmalıdır. Tankın periyodik bakımını yapmak ve temizlenmesini
sağlamak üzere her durulama tankının tabanında tahliye vanası bulunmalıdır.
Metal yüzeyinde kolaylıkla yıkanabilecek çeşitli maddeler bulunabilir. Mineral asit ve tuzlarını içeren çözeltiler kolaylıkla yıkanabilirken, özellikle çok viskoz elektropolisaj çözeltilerini durulamak zordur.
Durulama sularına hareket vererek parça hareketi sağlamak avantajlıdır. Siyanürlü ve alkali durulama çözeltileri kolaylıkla yıkanmaz; bunun için temizleme sonrası sıcak durulama yapılması(40 – 50 C0) oldukça sık rastlanan bir yöntemdir. Sis spreyleri alkali durulamalar sonrası tercih edilen yöntemdir. Bu tür bir yıkama, parça yüzeyindeki alkali çözeltinin sulandırılması yanında, parça üzerinde alkali kristallenmelerini önlemek için parçanın soğutulmasına da yardımcı olur. Yüzey-aktif kimyasallar doğaları gereği parça yüzeyine iyi tutunurlar ve çoklu durulama gerektirirler.
ASKILAMA
Kaplanacak parçalar, büyük yüzeyleri yere göre dik veya dike yakın olacak ve herhangi bir çukur oluşmayacak şekilde askılanmalıdır. Eğer bu mümkün değilse süzülme delikleri sağlanmalı, askı çıkarılırken eğlimeli, veya hava uygulanarak çözeltinin alınması gerekmektedir. Genelde, parçanın uzun kenarı yatay olarak ve eğer mümkünse birbirinin üzerine damlama yapmayacak şekilde askılanır. Askı izolasyonu yarık ve çatlaklarda çözelti birikimini önleyecek şartlarda olmalıdır. İzolasyon olmayan askılar, geniş yüzeylerde oluşan pürüz va ağaçsı kaplamanın kapilerlik etkisinden dolayı çok fazla çözelti tutmalarını engellemek için, temizlenmelidir. Askı eğer mümkünse çözeltilerden yavaşça alınmalı ve süzülme zamanı boyunca tank üzerinde bekletilmelidir. Manuel uygulamalarda tank üzerinde süzülme mili konulabilir; otomatik sistemlerde ortalama robot hızı ve kaplama zamanı göz önüne alınarak banyodan alınma hızı ve transfer zamanı ayarlanabilir.
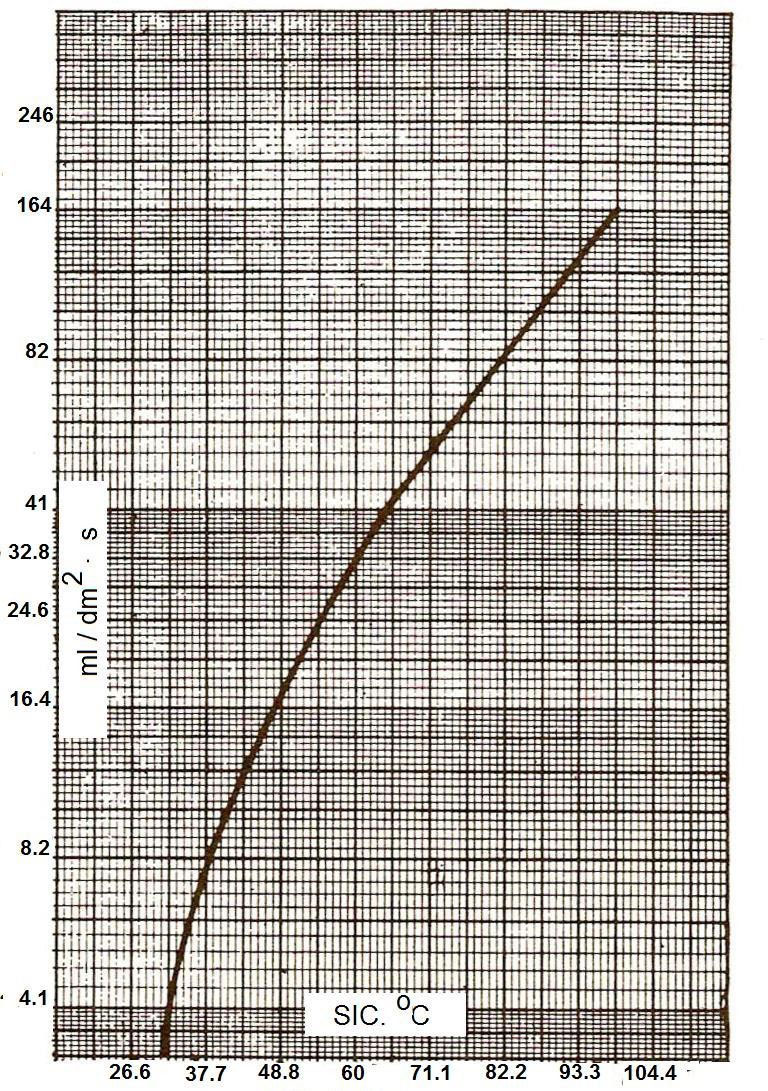
Parçaları sıcak çözelti bulunan tanktan çıkarken sis spreyleri ile, ve tankın içindeyken ıslatmak, elverişlidir. Bu hem taşınma kayıplarını, hem de buharlaşma kayıpları için kullanılan su miktarını azaltır. Şekil 8'de çeşitli sıcaklıklarda çözelti yüzeyinden buharlaşan suyun yaklaşık hacimleri gösterilmektedir. Özel proseslerde tank üzerine hava uygulamak da çözelti kayıplarını azaltmak amaçlı kullanılabilir, ancak her durum için uygun bir metod değildir.
ÇOKLU DURULAMA
Çoklu durulamanın avantajları şekil 2'de gözlenebilmektedir. Örneğin, durulama aralığı M, beslenen su oranı Y, taşınan çözelti hacmi D ve tek durulamada hacim 10 kabul edersek, bu durulamanın denge konsantrasyonu taşınan çözeltinin % 9'u olacaktır (Ce/C0 = 0,09).
Şekil 8. Su yüzeylerinde buharlaşma, ml/dm2 . s
Fakat, eğer iki veya üç durulama, tek durulamayla aynı miktarda su kullanımıyla, ayrı su beslemeleriyle kullanılırsa, son durulamanın denge konsantrasyonu % 2,8 veya % 1,2 olacaktır.
Aynı miktar su kullanımıyla seri durulamalar ters-akışlı durulamaya çevrilirse son durulama sularının konsantrasyonları, sırasıyla % 0,9 ve % 0,085 olacaktır. İstenen son durulama konsantrasyonu, taşınan çözelti konsantrasyonunun % 0,1'inin altındadır. Şekil 2'ye göre hesaplanan göreceli su gereksinimleri tablo 2'de verilmiştir.
Durulama çeşidi | Tek | Seri | Ters-akışlı |
Banyo numaraları | 1 | 2 | 3 | 2 | 3 |
Beslenen toplam su Q, lpm | 10 | 0,61 | 0,27 | 0,31 | 0,1 |
Tablo 2. Son durulama suyunun konsantrasyonunun(Ce), içeri taşınma konsantrasyonunun(C0) %0,1'i olması için gerekli toplam durulama suyu hacmi (her durum için içeri taşınma hacmi dakikada 0,01 l olarak alınmıştır)
Böylece, ikili ters-akışlı durulamanın üç ayrı su beslemeli durulamayla hemen hemen aynı tesiri gösterdiği ve her durumda tek durulamadan etkili olduğu görülmektedir. Manuel işlemler için ters-akışlı durulama sistemini basitçe tasarlamak alışılagelmiştir. Çünkü bu durumda çözelti seviyesinin pek önemi yoktur. Aynı zamanda tek durulamayı ikili veya üçlü ters-akışlı durulamaya çevirmek tankların arasına birkaç set kaynatılmasıyla mümkün olabilir. Ters-akışlı durulamaların tam otomatik sistemler için düşünülmesi durumunda durulama tankları arası pompa kullanılabilir. Bu yolla doğru çözelti seviyeleri ve iyi karışma için arzu edilen su beslemelerinin tankın tabanından yapılması sağlanabilir.
SPREY DURULAMA (DUŞLAMA)
Eğer parça üzerindeki kirliliğin sulandırılması için göreceli olarak az su kullanılıyorsa sprey durulama çok etkili bir durulama olabilir. Eski kuruluşlarda, prosesler arası tek durulamanın olduğu durumlar için oldukça etkili bir yııkama tekniğidir. Sprey durulamada saf su kullanılması durumunda , bir sonraki proses banyosunun içine istenmeyen ürünlerin karışması oldukça azalır.
Sprey durulamada kullanılan suyun etkinliği çok önemlidir. Spreyin yalnızca parçalar uygun pozisyondayken çalışması, başlıkların suyu tüm parçalar üzerine homojen olarak püskürtecek ve kullanılan suyun hacmini kontrol edecek şekilde tasarlanması gereklidir. Sıklıkla kullanılan bir veya daha fazla delikli boru bu bakımdan yetersiz kalmaktadır.
En etkili sprey bile bazen parça ya da askı üzerindeki girintilere erişemeyecği için bir de daldırma durulama kullanılmalıdır. Spreyin daldırma durulama tankının üzerine konuşlandırılması ve parçaların tanktan ayrılırken spreye maruz bırakılması sıklıkla kullanılmaktadır. Bu ters-akışlı durulamalara, tüm taze su sprey vasıtasıyla sağlandığı zaman, yüksek verimlilik sağlar. Sıçrama, basınçlı suyun askıları düşürmesi gibi etkenlerden dolayı püskürtülen suyun limitli kullanılması gereken çoğu durumda, gerekli suyun bir miktarı direk tanka verilmek suretiyle besleme yapılır. Özellikle otomatik kaplama tesislerinde sisteme parça banyodan alınırken çalışan spreyler konulması önemlidir.
SU EKONOMİSİ:
Suyu ekonomik olarak kullanmak için uygulanan yöntemler:
- Çoklu ters-akışlı durulama 2- Sprey durulama 3- Sprey ve daldırma durulama
Eğer spreylere gelen su, tank dibinden pompa yardımıyla beslenirse de ilave su tasarrufu sağlanır. Bazı işletmelerde (kaliteyi arttırmak üzere) suların soğutulması veya ısıtılması gerektiğinde, su ekonomisi daha da önem kazanır. Sonuçta bu suların çeşitli yöntemlerle ıstılması veya soğutması ciddi maliyetlerle mümkündür.
Bazı tesislerde ise, kullanılan suların atılmadan önce durulama suları olarak kullanılması da su tasarrufu sağlar. Özellikle çökme gibi istenmeyen etkilerin görülmeyeceğinden emin olunduktan sonra, bir durulama suyu başka bir durulamaya pompa yardımıyla alınabilir.
Örneğin nikel kaplama sonrası durulama suyu nikel kaplama öncesi asit çözeltisinin durulama suyu olarak kullanılabilir. Bununla birlikte aynı su alkali temizleme çözeltilerinden sonraki durulama suyu olarak, nikel hidroksit vs. gibi çökeltiler oluşacağı için, kullanılamaz. Sıcak yağ alma gibi sıcak çalışan banyoların üzerinde kullanılan yoğunlaştırıcı yardımıyla, buharın yoğunlaştırılmasıyla elde edilen su, durulamalarda kullanılarak da su tasarrufu sağlanabilir.
Öncelikle sulandırma oranı bilinirse, ekipmanlar kirlilik konsantrasyonunu minimum atıkla istenilen düzeye düşürecek şekilde kurulabilir. Örneğin zaman kontrollü bir selenoid vana yardımıyla tanka her yüklemede miktarı ayarlı su verilmesi sağlanabilir. Zamanlayıcı, bir ayak pedalı, limit düğmesi ya da otomatik sistemlerde bilgisayar kontrolüyle aktif hale getirilebilir. Eğer su beslemeleri değişik oranlarda yapılıyorsa, kirlilik konsantrasyonu arttığında su beslemesini arttıracak iletkenlik kontrolörü bağlamak uygun olabilir. Ayrıca, su besleme miktarında istenmeyen dalgalanmaları engellemek üzere, taze suyun akışını yönetecek basit bir tesisat cihazı olan akış sınırlayıcıları bağlamak her zaman faydalı olacaktır.
DURULAMA SİSTEMLERİNİN TASARLANMASI
Etkili durulama sistemlerini tasarlamak, prensiplerini anlamayı, spesifik amaçları dikkatlice düşünmeyi, kurulumun detaylarına dikkat etmeyi gerektirir
Durulama sistemleri tasarlanırken amaç; durulamanın yeterli olması, su tasarrufu sağlanması, oluşan atık miktarının azaltılması, kimyasal tasarrufu, atık sisteminin boyutunu ve maliyetini azaltmak veya yukarıdaki parametrelerin kombinasyonlarını sağlamak olmalıdır. Durulama prensiplerinin uygulamalarının, yeni tesis kurulumlarda kullanılması Kushner, Zabban, ve Hanson tarafından aşağıdaki adımlarla açıklanmıştır:
- Tablo 1'e göre birim alan başı taşınmayı ve saatte işlem görecek yüzey alanını hesaplanır. Bu hesaplama, kirlenme, taze su beslemesi yapılmadan parça askılarının sayısı ve durulama suyunun bir bileşene göre analizinin yapılmasıyla da yapılabilir. Dolap kaplama için de taşınmanın belirlenmesinde mümkün olan yöntem budur.
- Her son durulama için izin verilebilecek kirlilik miktarı belirlenmelidir. Kaynaklarda bulunabilecek bazı durulama banyoları için değerler aşağıdadır;
Nikel(Bakır ya da diğer ağır metallar için) sonrası durulama 37 ppm Siyanür sonrası durulama 37 ppm
Krom sonrası durulama 15 ppm
Asit daldırma sonrası durulama 750 ppm
Alkali temizleme sonrası durulama 750 ppm
Krom öncesi asit daldırma durulaması 15 ppm
- Durulaması yapılacak proses banyosunun kompozisyonu ve bu bilgilerden yararlanarak durulama kriteri hesaplanmalıdır. C0/Cr.
- 1,2 veya 3 ters-akışlı basamaklı durulama için, her durulama banyosuna gerekli su miktarı (Q), şekil 1 kullanılarak, ya da (6)'cı eşitlik çözülerek hesaplanabilir.
Q = D/M n√C0/Cr [6(b)]
Her durum için kullanılmak üzere durulama sayısı, en ekonomik olacak şekilde ve ilave ekipmanları ile işletme maliyetlerini göz önüne alarak seçilmelidir.
- Toplam sarfiyatı tahmin etmek için, her durulamanın sarfiyatı toplanmalı ve güvenlik faktörüyle çarpılmalıdır. (2 önerilir)